切削加工とは?定義・分類から工具・条件まで
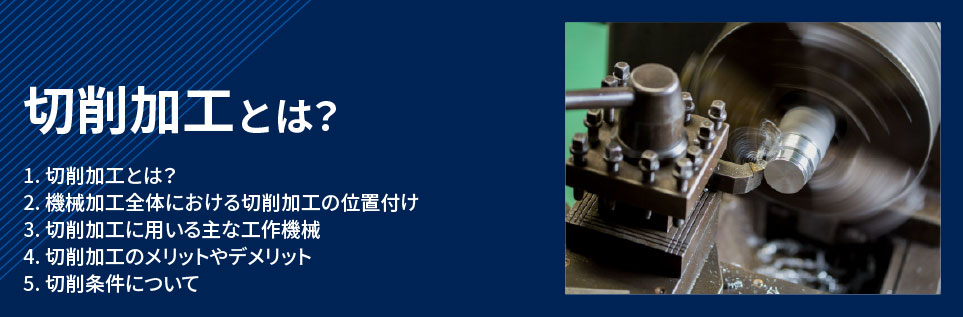
切削加工は金属や樹脂などの材料を削って形を作る加工法で、機械加工の代表的手法です。
本記事では、切削加工の定義や機械加工全体での位置付け、使用される工作機械の種類やメリットデメリット、さらに加工条件(切削条件)の設定項目を分かりやすく説明します。
目次
切削加工とは?
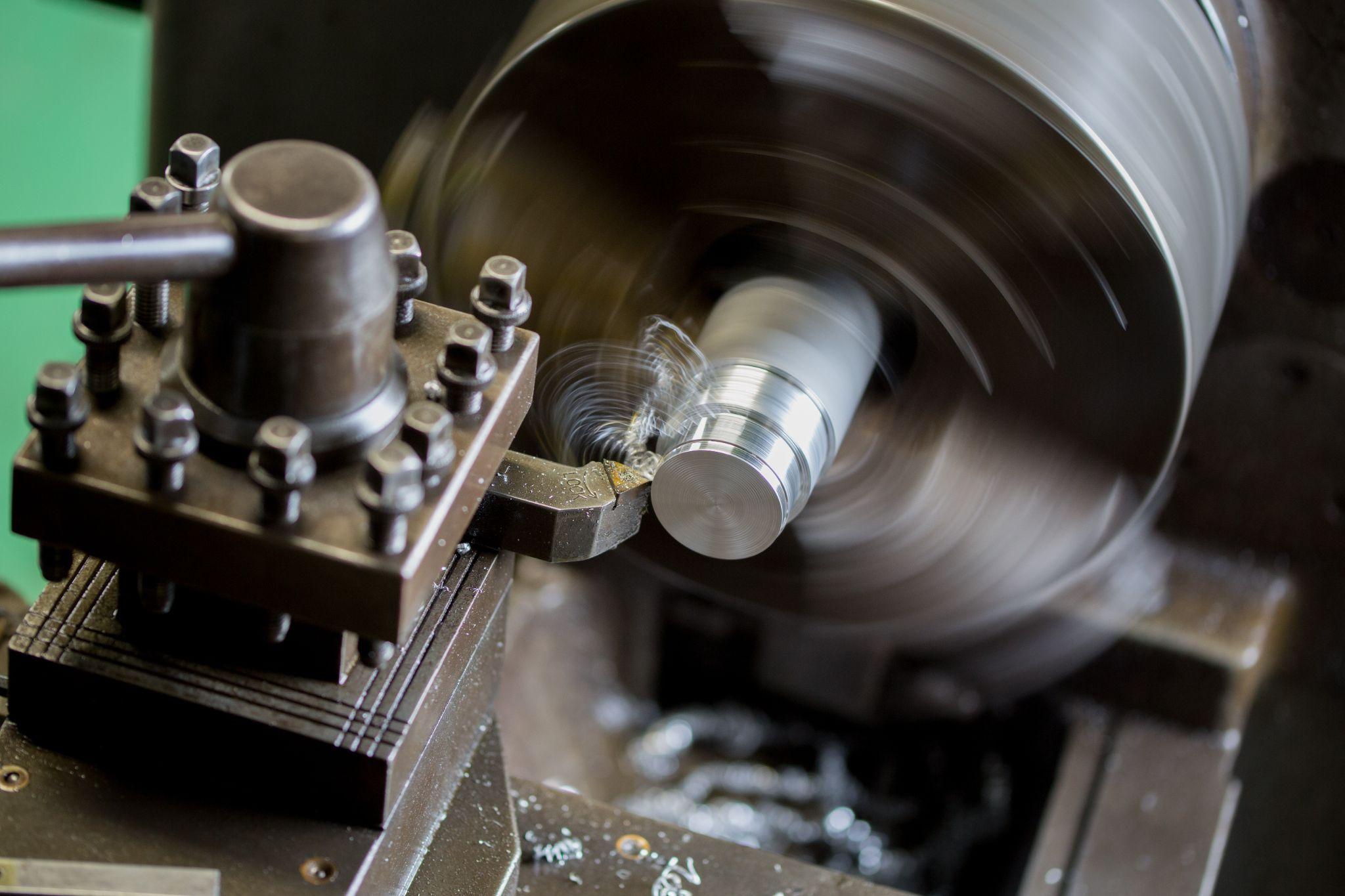
切削加工(せっさくかこう)とは、切削工具と呼ばれる刃物を用いて素材の一部を削り取り、目的の形状に加工する方法です。
一般的に旋盤やフライス盤などで金属を削る加工を指し、木材やプラスチックの切削にも用いられます。切削加工は除去加工とも呼ばれ、素材を削り取って成形する点が特徴です。
一方、大きな力で素材を変形させて形を作る塑性加工(鍛造やプレスなど)とは原理が異なります。
機械加工全体における切削加工の位置付け
機械加工は、その加工原理によりいくつかのカテゴリに分類できます。
大別すると、材料を削って形を作る「除去加工」、材料に力や熱を加えて変形させる「成形加工(変形加工)」、複数の部品を繋ぐ「接合加工」の三種類があります。
加工の分類 | 主な加工法の例 | 概要 |
---|---|---|
除去加工 (材料の除去による加工) | 切削加工(旋盤加工・フライス加工・穴あけ加工)、研削・研磨(グラインダー、砥石による加工)、放電加工 など | 工具や砥石で素材を削り取って形状を作る加工法。高い寸法精度の部品加工が可能。切削加工は除去加工の代表例。 |
成形加工 (塑性変形・鋳造による加工) | 鍛造、プレス加工、板金曲げ、鋳造、射出成形 など | 素材に大きな力や熱を加えて変形させ、型に沿った形状を作る加工法。素材を削らないため材料歩留まりが良い。金型を用いる加工が多い。 |
接合加工 (材料同士の結合) | 溶接、ろう付け、接着、リベット止め など | 複数の部品や材料を接合して一体化する加工法。部品同士を繋ぐことで複雑な製品を構成する。 |
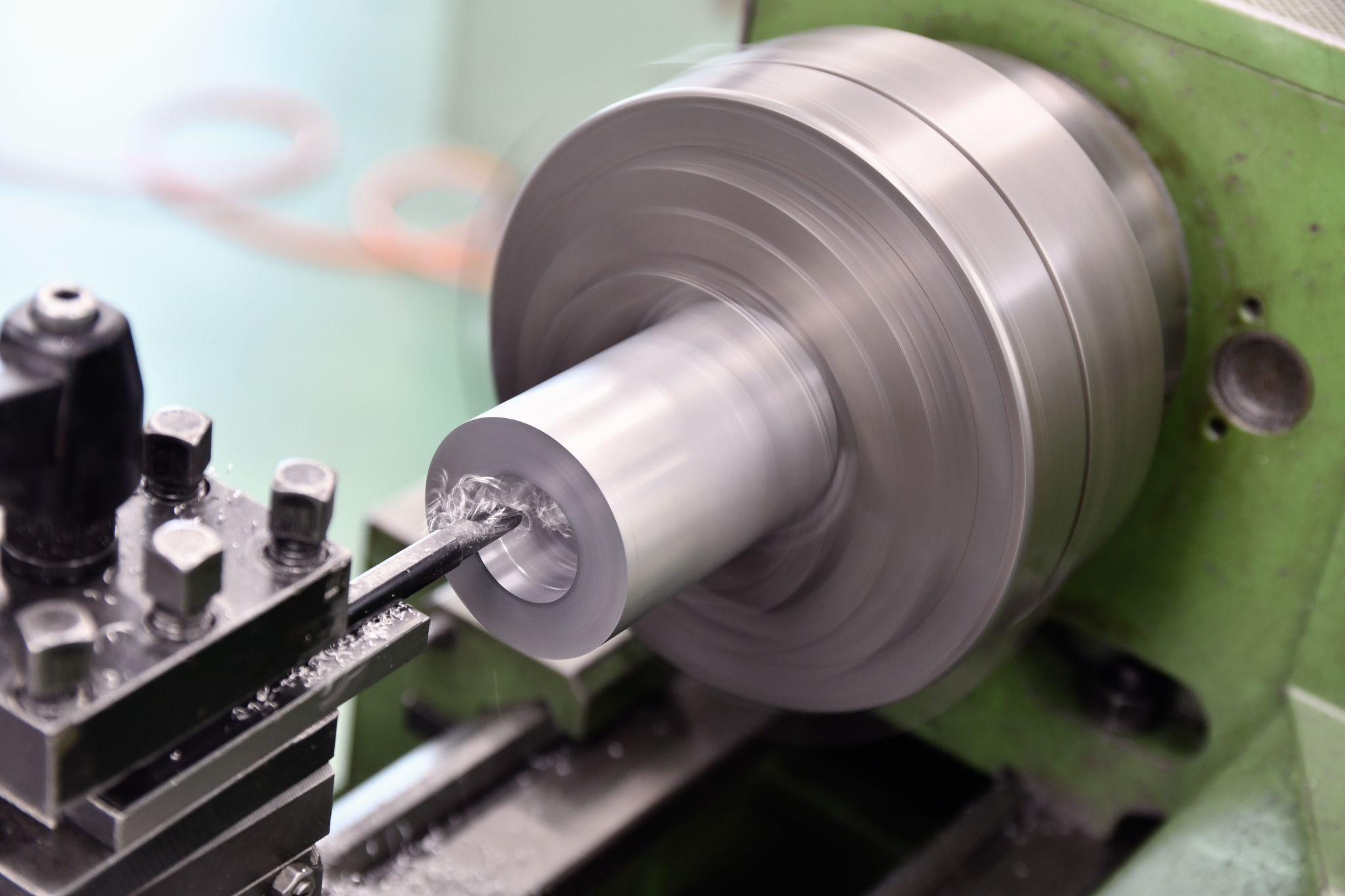
除去加工
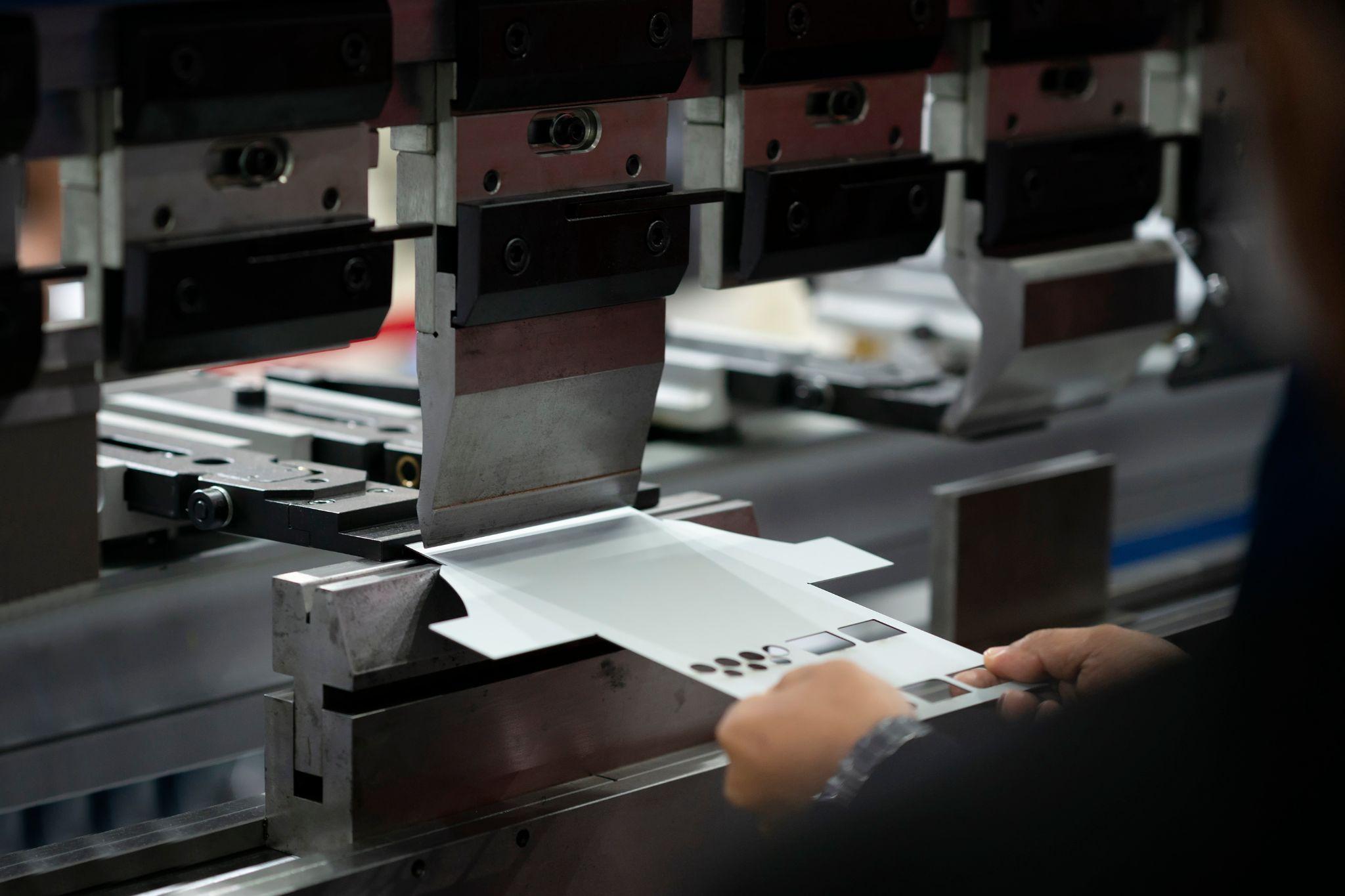
成形加工
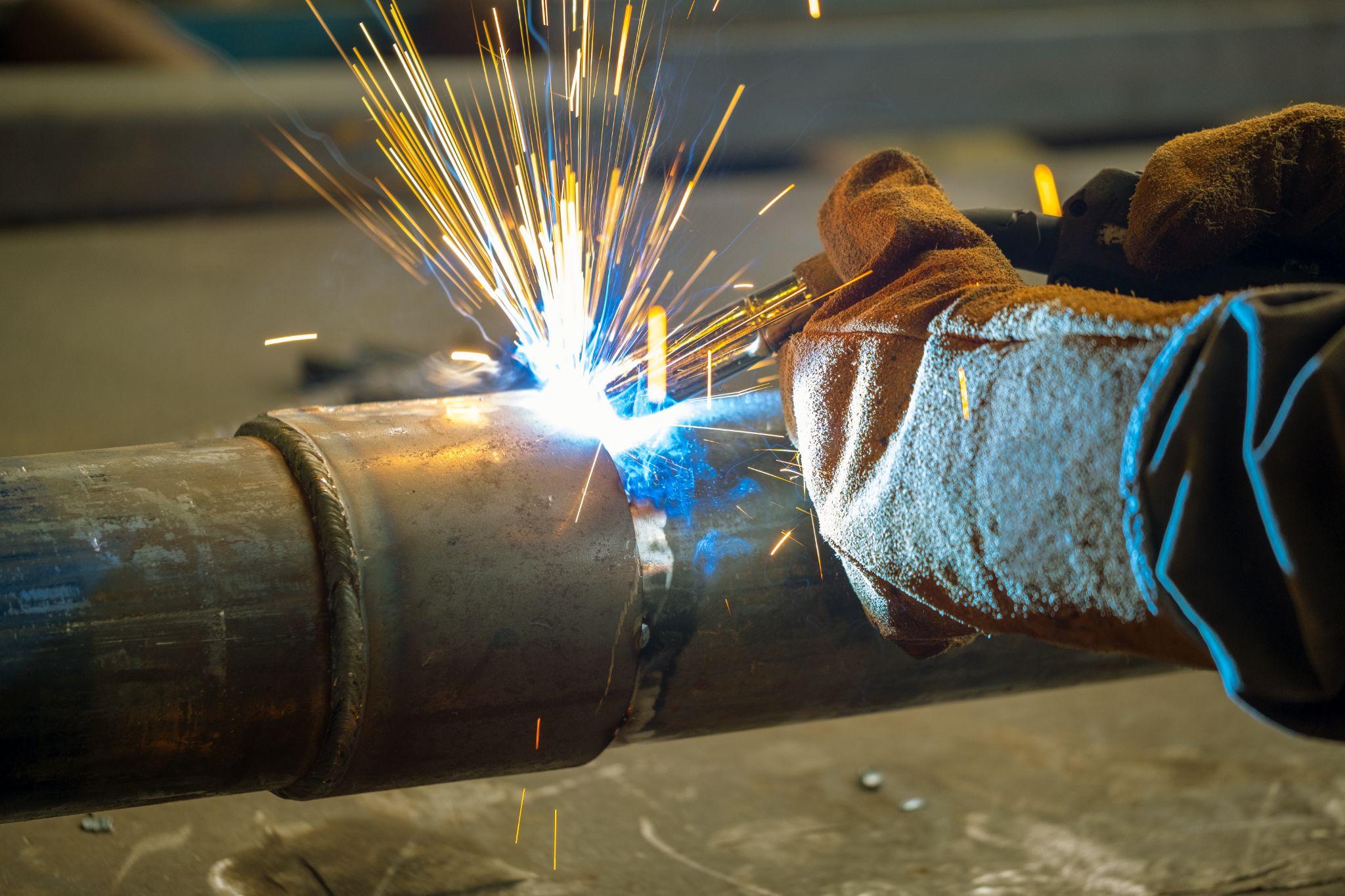
接合加工
上表のように、切削加工は「除去加工」に分類されます。除去加工には切削のほか研削(研磨)や特殊加工も含まれますが、切削加工は除去加工の中でも基本かつ中心的な存在です。
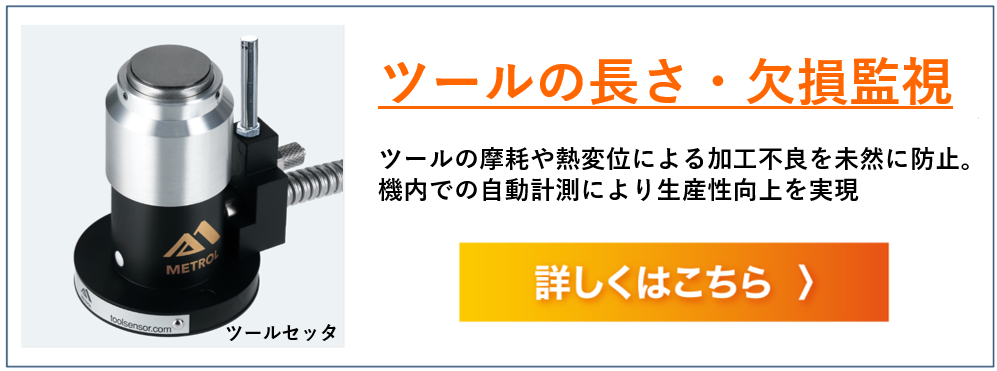

切削加工に用いる主な工作機械
切削加工を行うには、工作機械と呼ばれる専用の機械装置を使用します。
代表的な切削用工作機械として、旋盤・フライス盤・マシニングセンタの3種類が挙げられます。
旋盤
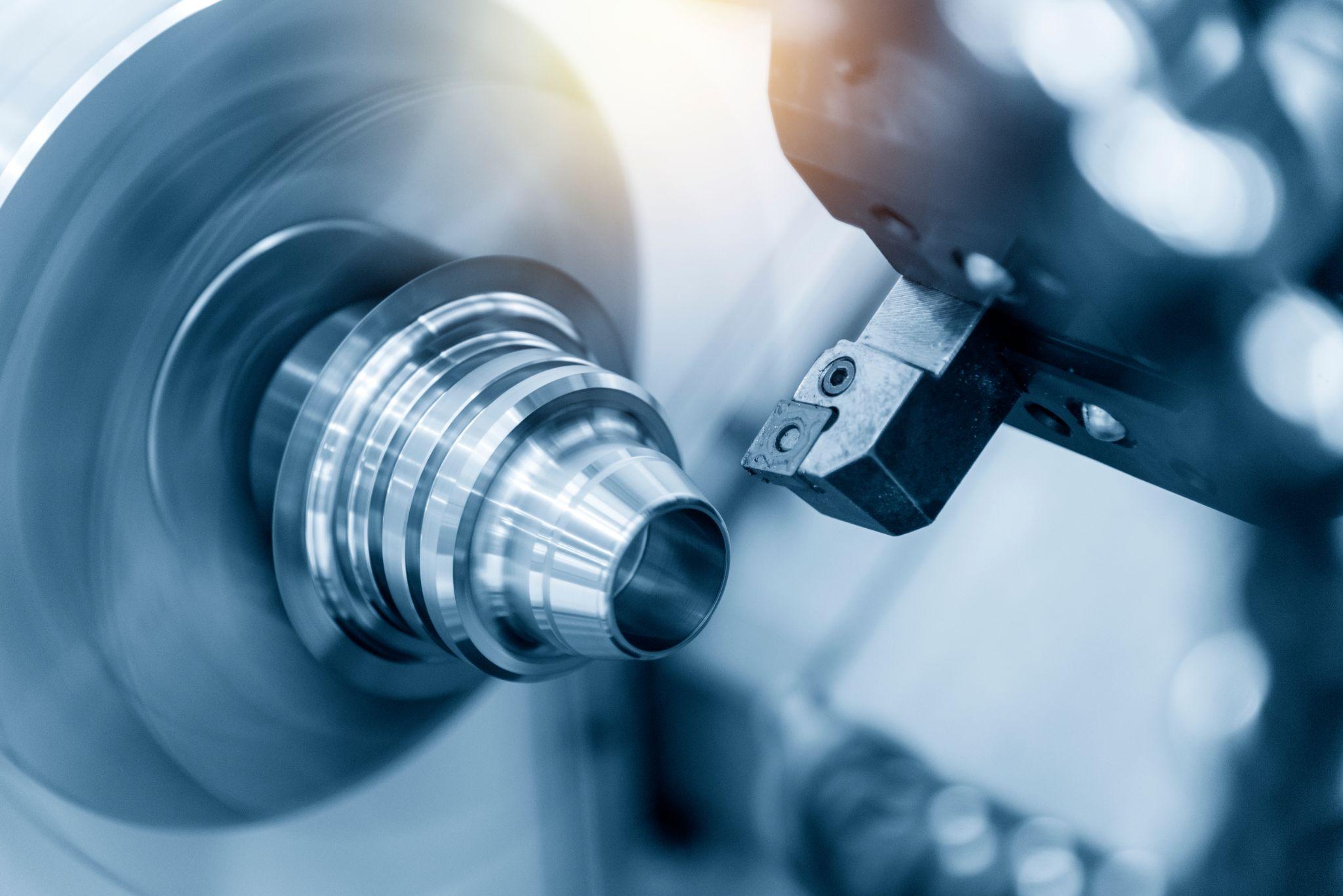
旋盤(せんばん)は、工作物(素材)を高速回転させ、固定した刃物(バイト)を当てて削る工作機械です。
工作物が自転し、工具は主に直線方向に送りを与えながら加工を行います。旋盤では素材が回転軸に対して対称形状(回転対称形状)に加工されるため、円筒形や円盤形状の加工に適しています。
旋盤はシャフト(軸)や円柱状部品の外径削り(外丸削り)、穴の中を広げる中ぐり(ボーリング)、端面の切削、ねじ切り加工、溝切り、部品の切断(突っ切り)など多彩な加工が可能です。
フライス盤
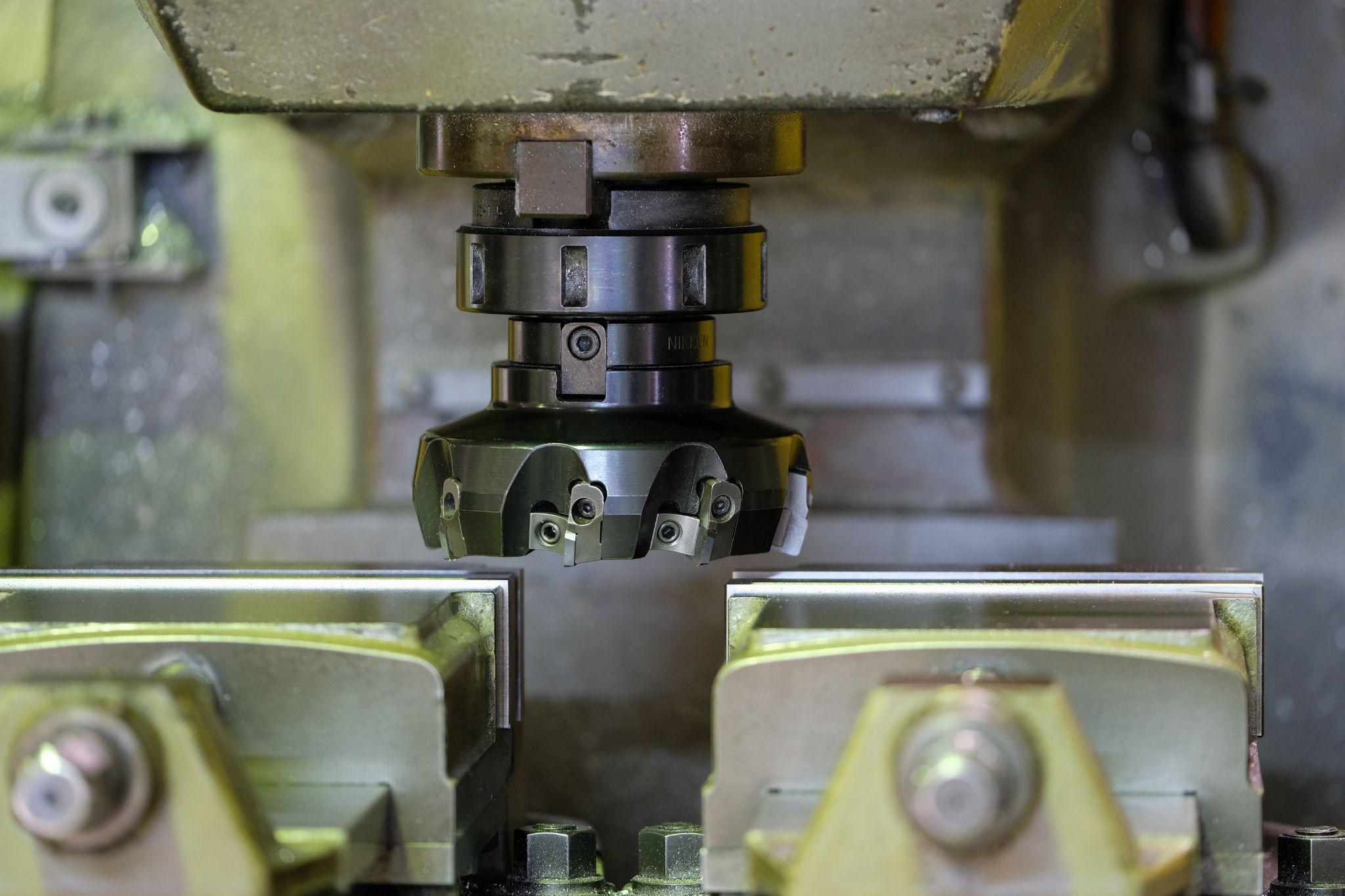
フライス盤は、回転する刃物(フライスカッター、エンドミル)を工作物に押し当てて削る工作機械です。
旋盤とは逆に、こちらは工具側を回転させ、工作物はテーブル上に固定して加工を行います。
工具が回転しながら素材を削り取ることで、平面や溝、穴あけなどの加工に適しています。特に四角いブロック状の材料(角物)の平面削りや側面切削、溝加工、段差加工などで威力を発揮します。
フライス盤では主軸にエンドミルやカッターと呼ばれる多刃工具を装着します。テーブルにバイスなどで固定した素材に対し、エンドミルを高速回転させて所定の経路で削ります。
マシニングセンタ
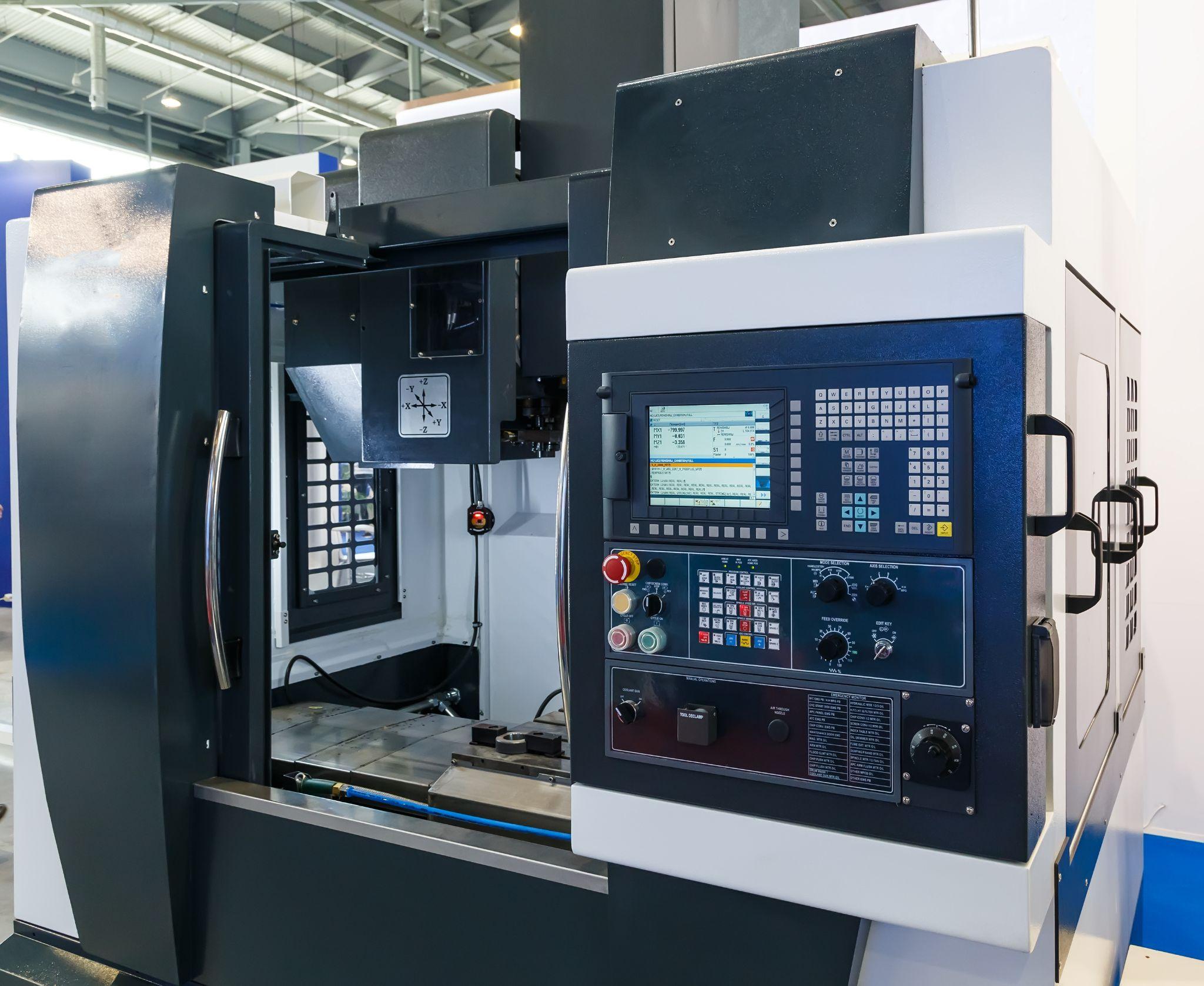
マシニングセンタは、自動工具交換機能を備え、多様な切削加工を連続して行えるNC工作機械です。
基本的にはNCフライス盤の発展形で、工具マガジンに多数のエンドミルやドリルなどを搭載し、プログラムに従って自動で工具を交換しながらフライス、穴あけ、中ぐり、ねじ切りなど複数の加工工程を1台でこなします。
加工精度と生産性を両立するために開発された、高度に自動化された工作機械です。
マシニングセンタでは、工作物は固定テーブルまたは可動テーブル上にセットされ、主軸に取り付けた工具が高速回転して加工します。
NC装置によりX、Y、Z軸の精密な制御が行われ、必要に応じてテーブルや主軸を回転・傾斜させる多軸制御(3軸~5軸制御)も可能です。
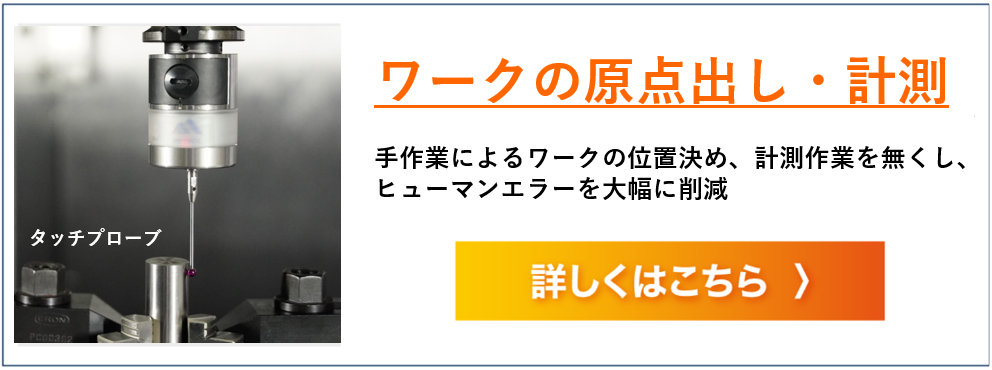

切削加工のメリットやデメリット
工具を押し当て、切り粉を排出しながら目的とする形状に加工する「切削加工」の主なメリットやデメリットを紹介していきます。
メリット①|低コストで高精度な製品の加工が可能
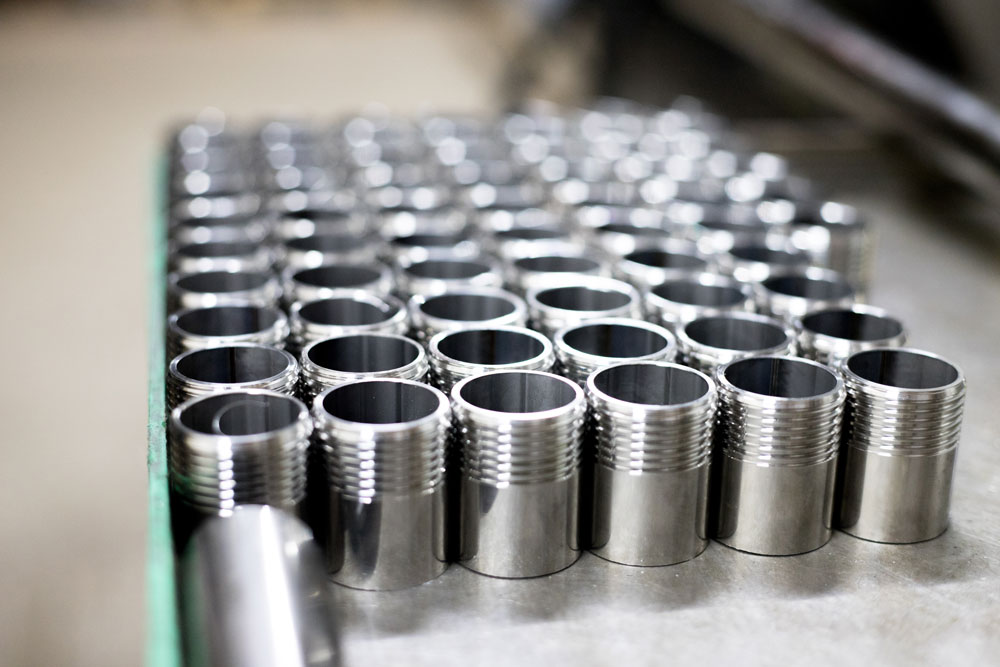
無垢の材料から任意の形状に除去加工する切削加工は、低コストで高精度な製品の加工が可能です。
特に、鋳型や金型を必要とする鋳造品や鍛造品よりも短納期かつ低コストで加工ができるため、試作品や少量多品種の加工に適しています。
鋳造や鍛造では困難な高精度加工も、切削加工なら容易に実現できます。
メリット②|加工形状の自由度が高い
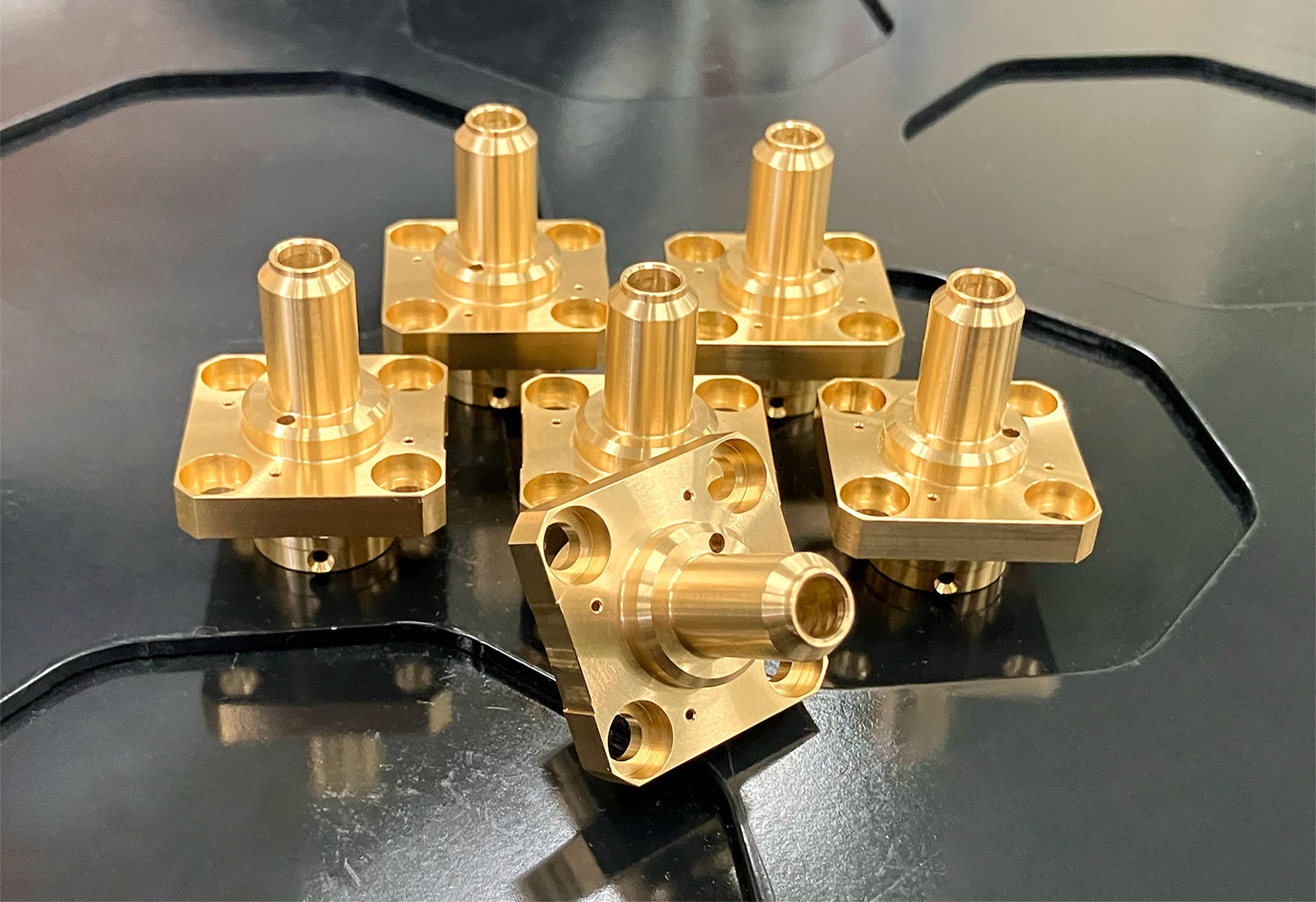
使用する工作機械の可動範囲内で加工できるものなら、加工形状の自由度が高いのも切削加工のメリットです。
プレスや板金などの場合は、使用する機械の出力によって加工できる「素材厚さ」に限界がありますが、切削加工なら問題ありません。
マシニングセンタやCNC旋盤などの工作機械を使用することで、手作業では困難であった形状も加工できるようになりました。
メリット③|被削材の制限が少なく、多様な材料に対応できる
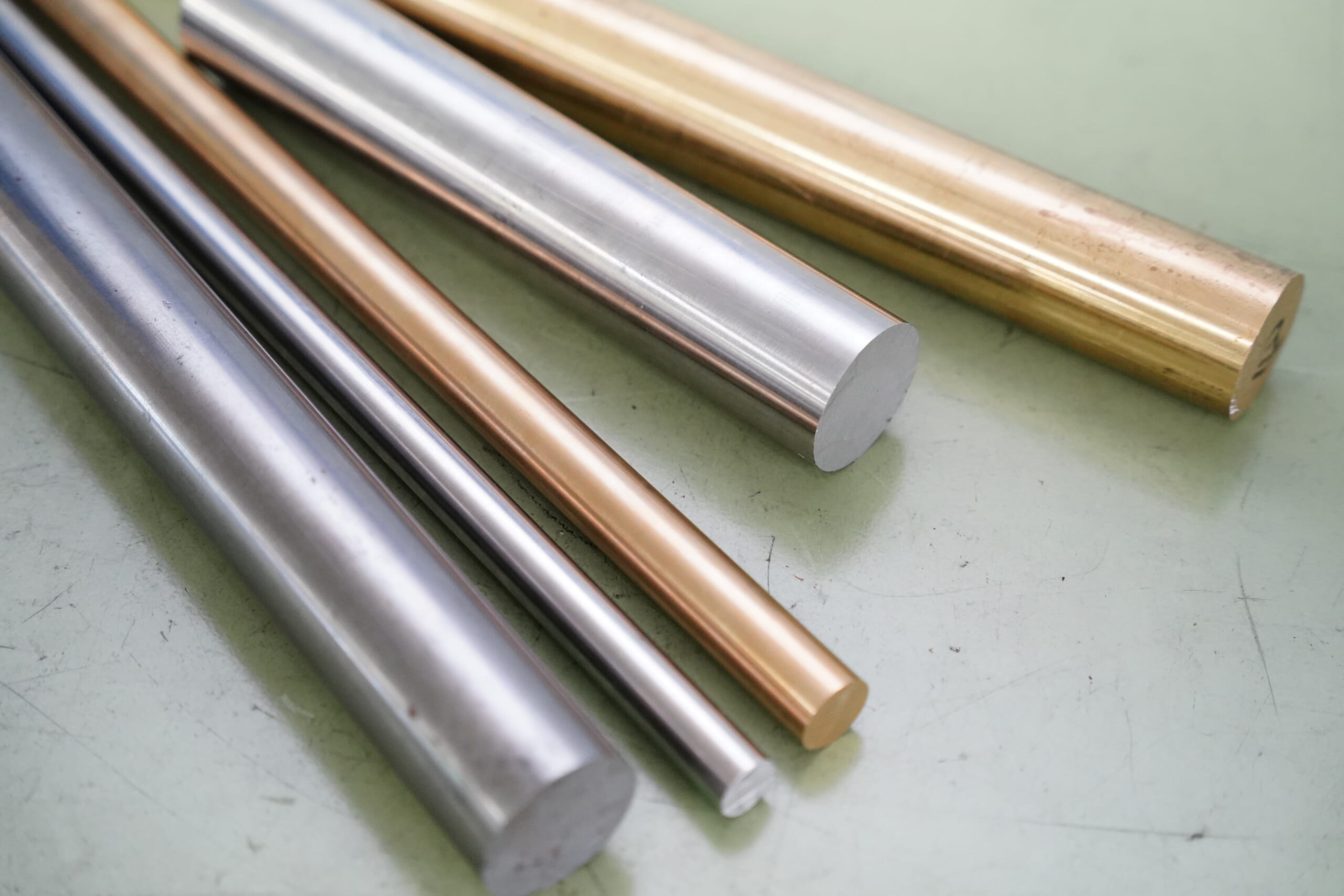
切削加工の強みは、鉄系金属やアルミ、銅、樹脂など、被削材の材質を選ばず加工できるということです。
適切な工具の材種や形状を選択すれば、木材や岩石なども切削加工ができます。
工具で切削可能なものであれば、多様な被削材に対応できるのが切削加工の大きなメリットです。
デメリット①|加工には作業者の技術が必要
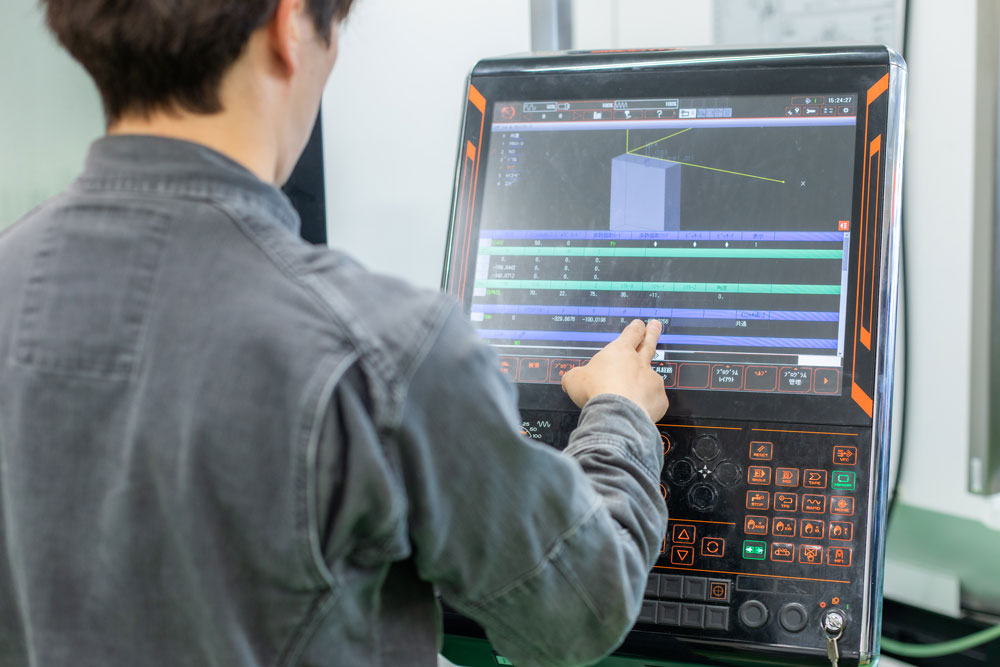
加工形状の自由度が高い切削加工ですが、高精度を要求する製品の加工には作業者の技術や高い熟練度を必要とします。
近年は、数値制御装置による加工が主流になっており「経験の浅い作業者でも複雑な形状の加工」ができるようになっていますが、高精度な製品の加工にはまだまだ熟練の技術が必要です。
材質や加工形状に適した工具の選定や加工方法の習得は、一朝一夕では得られません。
デメリット②|切り粉に関するトラブルはなくならない
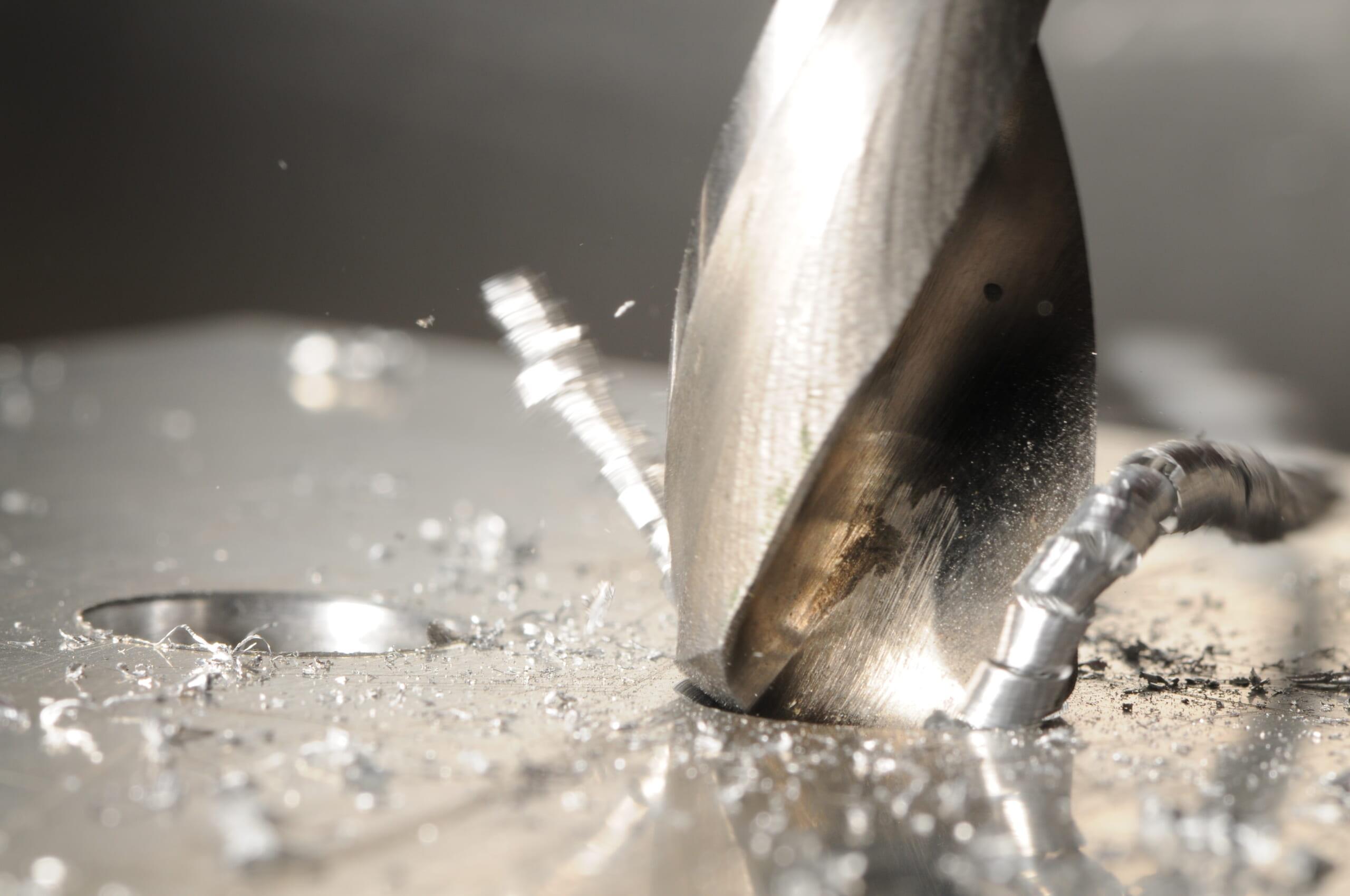
目的とする形状を得るために不要な部分を除去する「切削加工」では、切り粉に関するトラブルをゼロにはできません。
一般的に、切り粉は元の被削材よりも硬くなっており、工具の刃先に切り粉がかじり込むと刃先が損傷したり、摩耗が早くなったりします。
切り粉詰まりや構成刃先、加工面のキズ・工具の破損だけでなく、加工をおこなっている機械の事故・故障も「切り粉」によって引き起こされるトラブルのひとつです。
切削油の適切な供給やエアーブローを利用することで、切り粉によるトラブルを最小限におさえる工夫をしておきましょう。
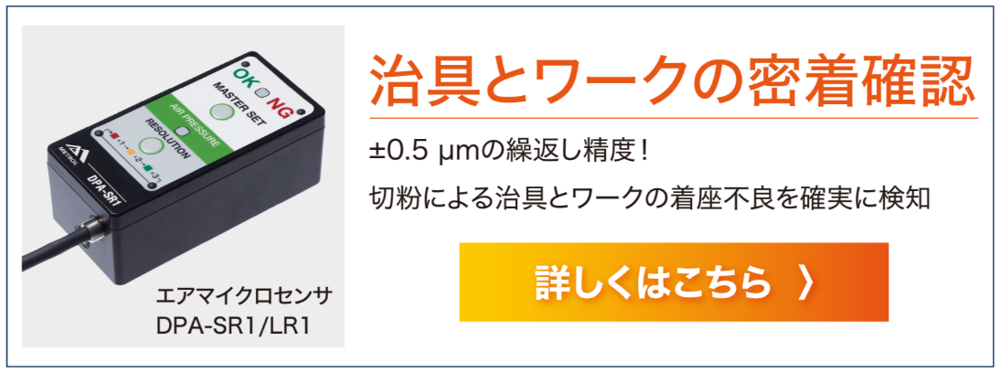

デメリット③|被削材や加工形状によっては、コストが高くなる
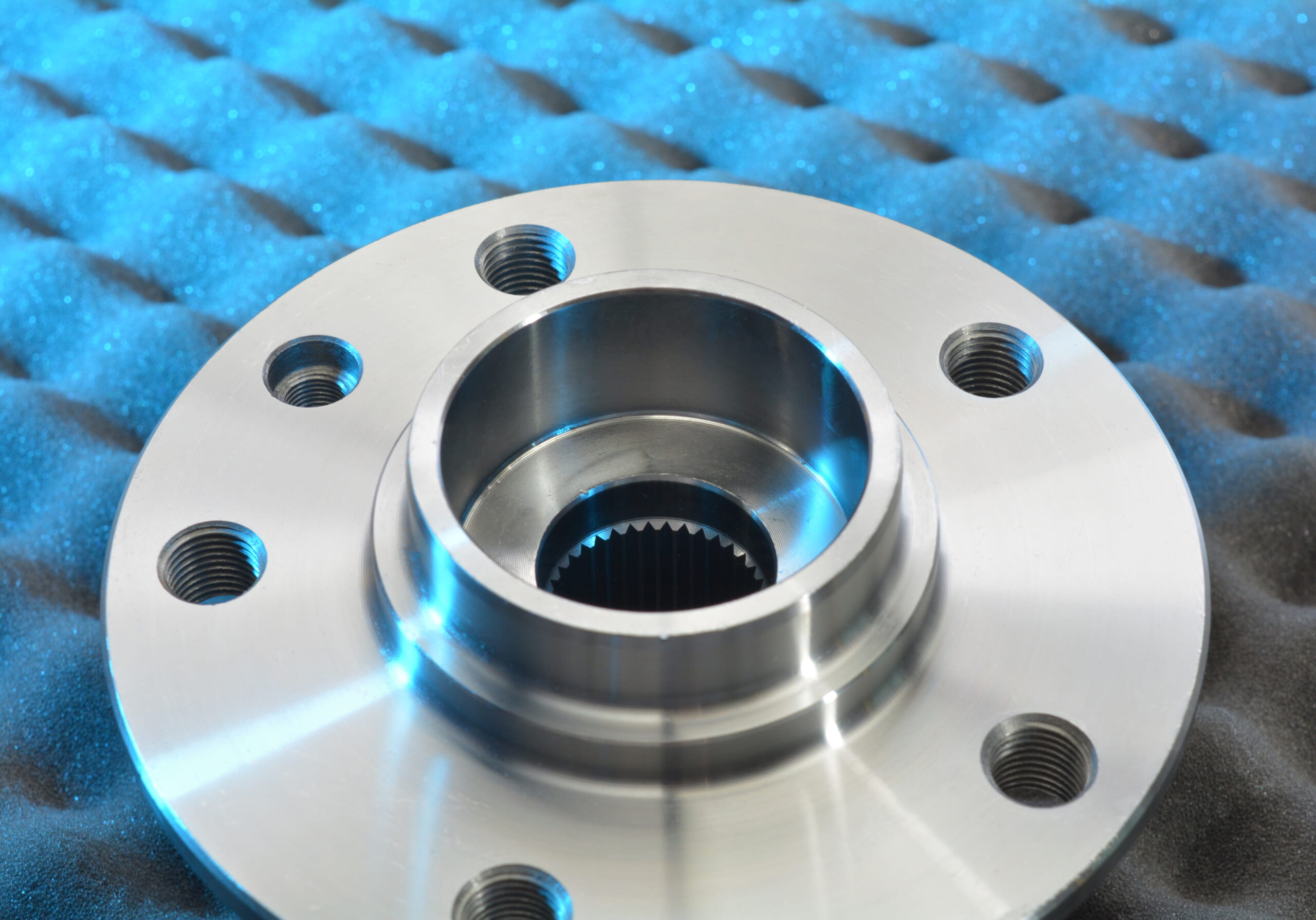
被削材の材質や加工する形状によっては、加工コストが高くなるのも切削加工のデメリットです。
例として、軸径に対して外径の大きなフランジ形状を持つシャフトなどは、切削量が多くなるため「切削にかかる時間」や「必要な工具(スローアウェイチップなど)」が多くなり、結果として加工コストが大きくなります。
過酷な環境で使用される部品や高硬度材の切削加工も、材料の価格や使用する工具が高額になるため加工コストは増大します。
切削条件について
切削加工を行う際には、工作機械や工具に対していくつかの切削条件(加工条件)を設定します。
切削条件とは、加工の進め方を数値で指定するもので、「切削速度」「送り速度(送り量)」「切込み量(切り込み深さ)」といったパラメータや、使用する工具の材質・コーティング、冷却剤(クーラント)の使用法などを指します。
切削条件の主な項目とその概要をご説明します。
切削速度(周速度)
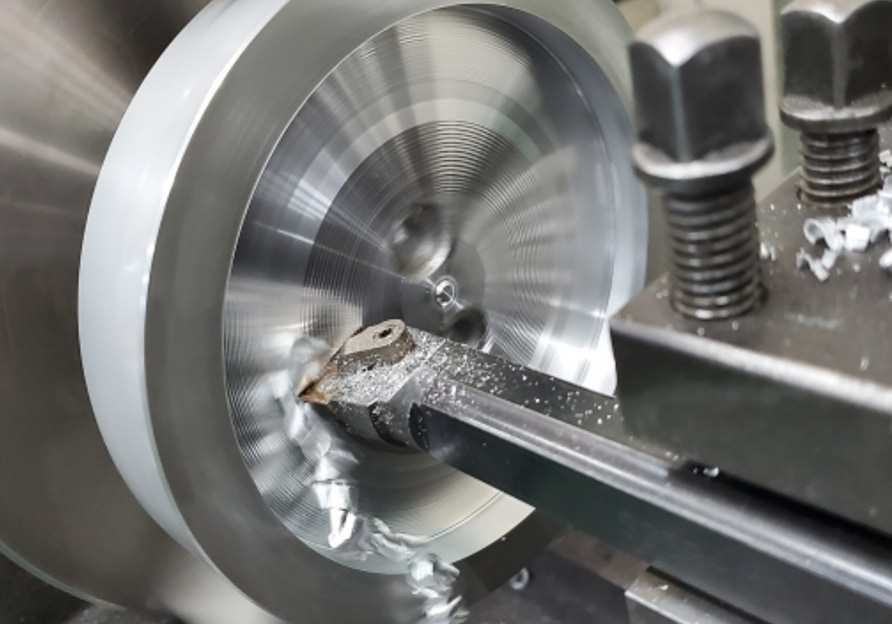
切削速度とは、工具が素材を切削する速度を表す値で、素材表面に対する相対的な滑り速度(m/minなどの単位)です。
例えば旋盤では工作物の回転によって刃物が素材を削る速度、フライス盤ではエンドミルの周囲が素材に当たる速度が該当します。
切削速度は工具材質と被削材によって適正値が決まります。
一般に工具が硬く耐熱性が高いほど高速な切削が可能です。切削速度が高すぎると工具先端が高温になり摩耗・焼損を招きますし、低すぎると加工時間が長く非効率になります。
適切な切削速度を設定することで、工具寿命を確保しつつ加工時間を短縮できます。
送り速度(送り量)
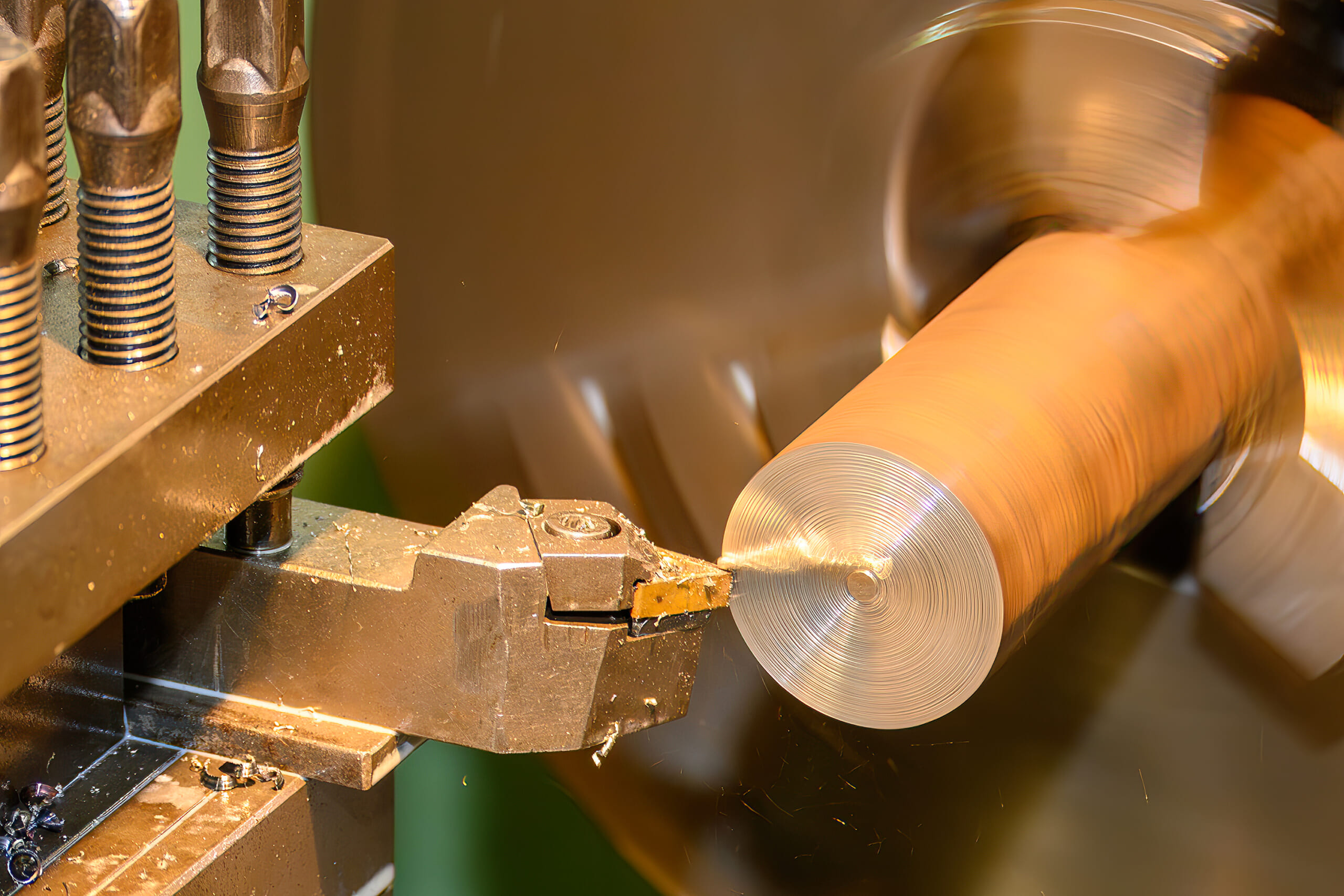
送り速度とは、工具または工作物を移動させる速度のことで、1分間あたりに進む距離(mm/min)で表されます。
旋盤ではバイトをどれだけ速く横送り・縦送りするか、フライス盤ではテーブルあるいは工具をどれだけ速く進めるかが送り速度です。
送りが大きい(速い)ほど1カットあたりに削る量が増え加工能率は上がりますが、その分切削抵抗が増して表面粗さが悪化したり、工具や機械への負荷が増大します。逆に送りを小さくすると精密で滑らかな切削面が得られますが加工時間は長くなります。
適切な送りの設定により、所望の表面仕上げを維持しつつ加工時間を短縮できます。
切込み量(切削深さ)
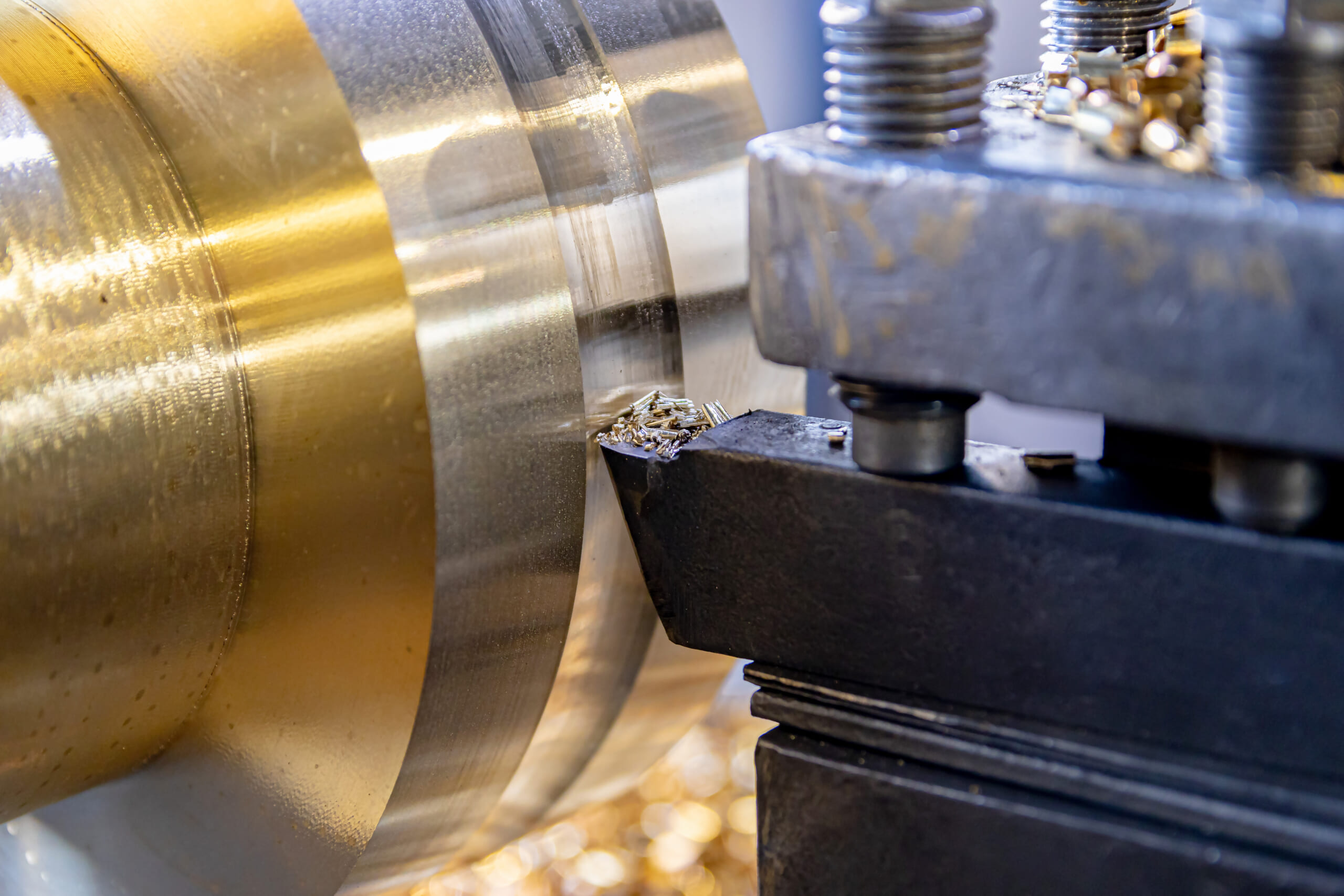
切込み量とは、工具が工作物に食い込む深さ(厚み方向の削り代)を指します。
たとえば旋盤の外径削りでは直径方向の削り代、フライスの平面削りでは刃物が素材に潜り込む深さが切込み量です。
切込み量が大きい(深い)ほど一度に除去する材料量が多くなるため加工は早く進みますが、その分工具への抵抗が大きく精度は低下しがちです。逆に切込みが小さいと加工負荷は軽く高精度になりますが、何度も層を削る必要があり加工時間が長くなります。
切込み量が過大だと工作物や工具がたわんで振動(ビビリ)を起こすことがあり、逆に極端に小さいと刃が材料をうまく捉えられず滑ってしまう場合もあります。
したがって工作物剛性や機械剛性を踏まえ、安定して切削できる範囲で適切な切込みを設定することが重要です。
工具材質
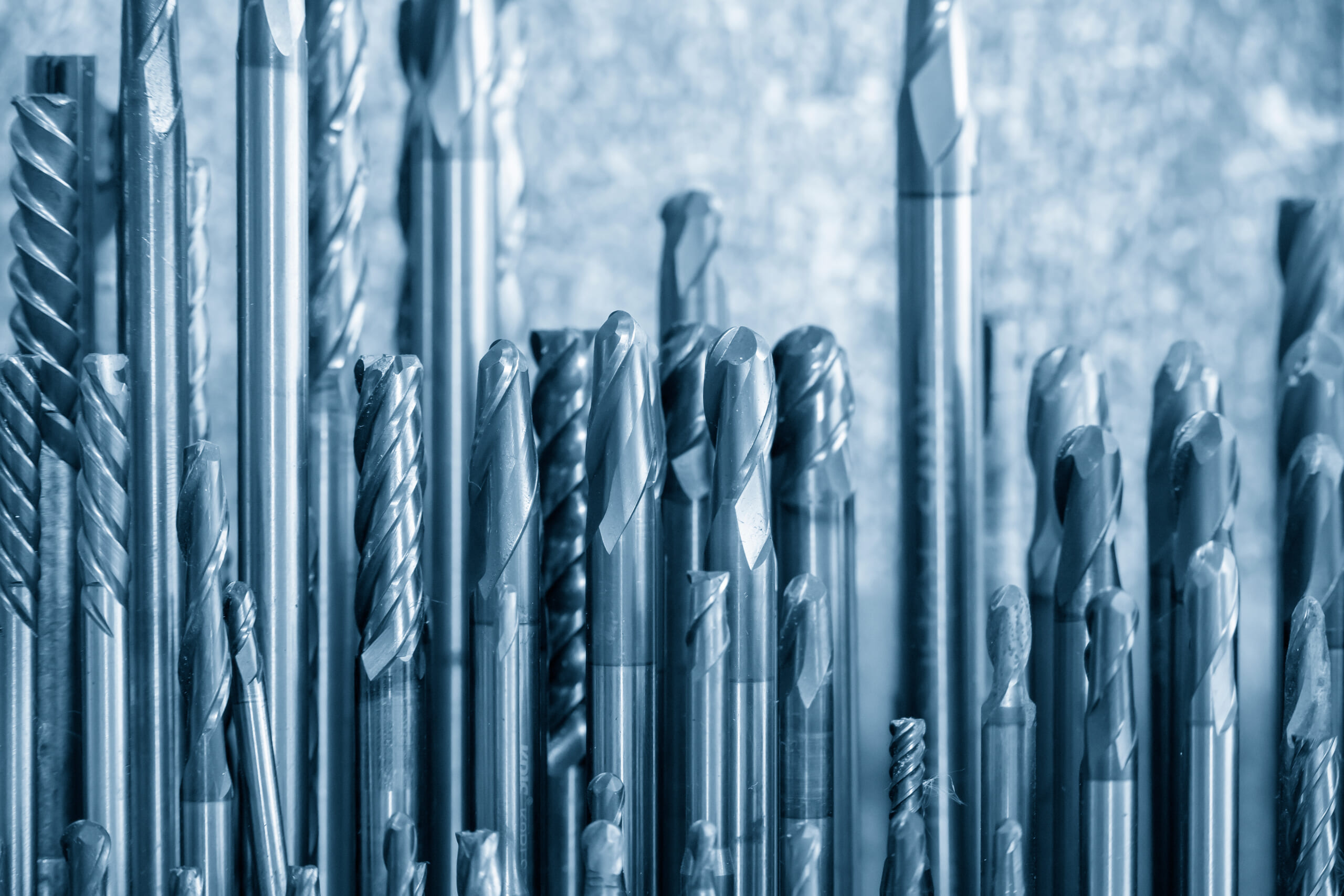
使用する工具の材質も切削条件に含まれる重要な要素です。
工具材質には、大きく分けて高速度鋼(ハイス)、超硬合金(硬質合金)、サーメット、セラミック、CBN(立方晶窒化ホウ素)、ダイヤモンド(PCD)などがあります。
それぞれ硬さや靱性、耐熱性が異なり、適する加工条件も違います。
一般的に、ハイスは靱性(粘り強さ)に優れ加工しやすい反面、耐熱性・硬度が低いため切削速度は抑えめに設定します。
超硬合金は硬度と靱性のバランスが良く高温にも強いため、ハイスより高速・高能率な切削が可能で、多くの現場で標準的に使われます。
セラミックやCBN工具はさらに高硬度で高温に耐え、硬度の高い焼入れ鋼などの加工や超高速切削に適しています。その代わり靱性が低く衝撃に弱いため、切込みや送りを小さくし安定した条件下で使用します。
ダイヤモンド工具(PCD)はあらゆる工具材の中で最も硬く摩耗しにくいですが、鉄系材料を高速切削するときの発熱や化学反応に弱く、主にアルミ合金や銅、樹脂、炭素繊維強化プラスチック(CFRP)など非鉄材料の高速加工に用いられます。
冷却・潤滑方法
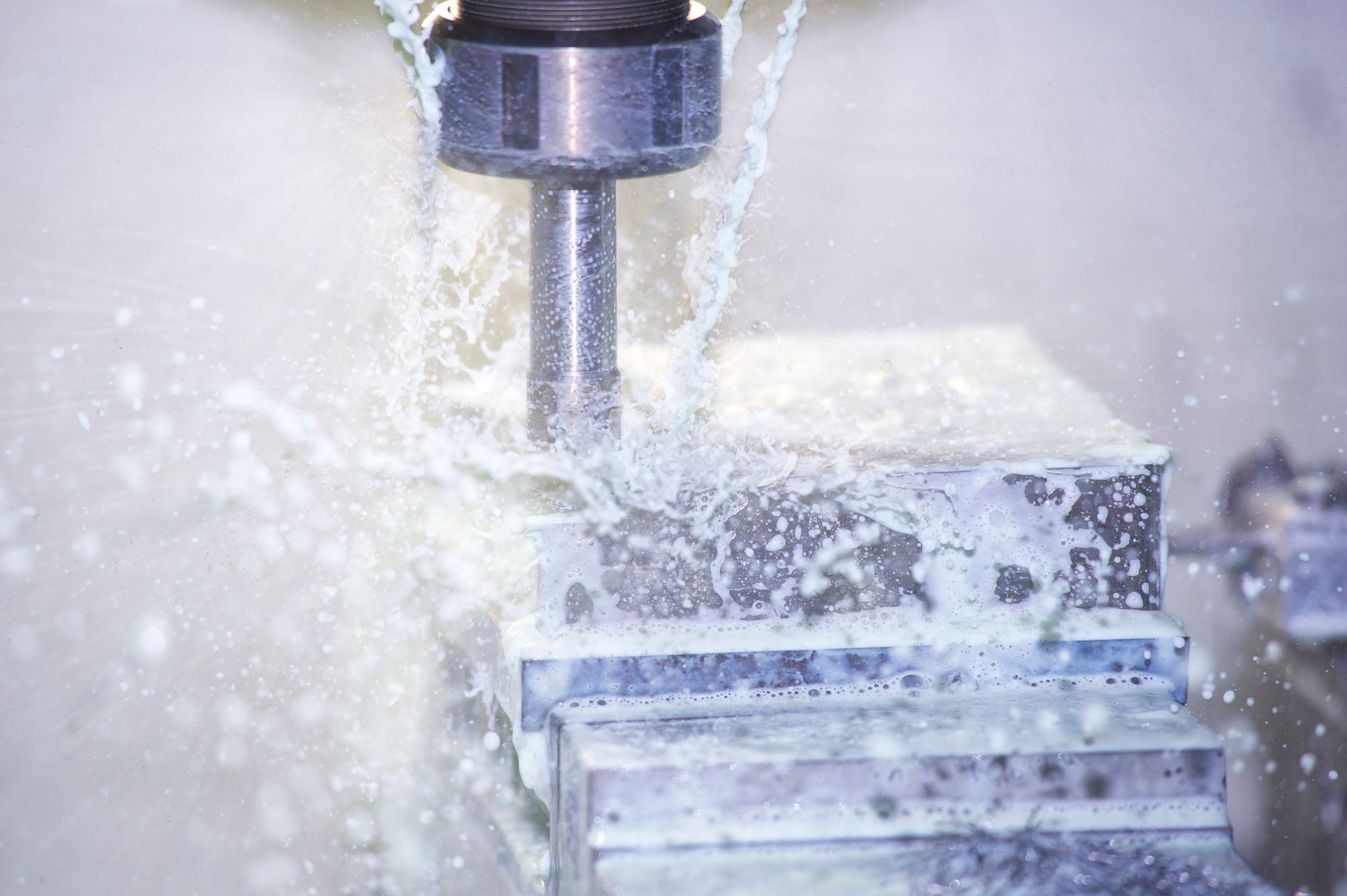
切削加工では、切削液(クーラント)や切削油を用いて加工部を冷却・潤滑することが一般的です。
切削時には工具と工作物の摩擦により高熱が発生し、工具摩耗や寸法誤差の原因となります。冷却液を噴射することで刃先を冷やし、熱による影響を抑えることができます。
また潤滑効果により摩擦抵抗を減らし、切りくずが滑らかに排出されるようサポートします。
メトロールの高精度な位置決めセンサとは?
切削加工の現場では、微細な形状や複雑な輪郭を高精度で削り出すために、部品の位置決めが極めて重要です。
製造工程の効率化・自動化が進む中、わずかなズレも最終製品の品質に大きな影響を与えるため、精密な位置決めが求められます。
ここで登場するのが、メトロールの提供する最新の位置決めセンサです。
高精度位置決めタッチスイッチ(位置決めセンサ)
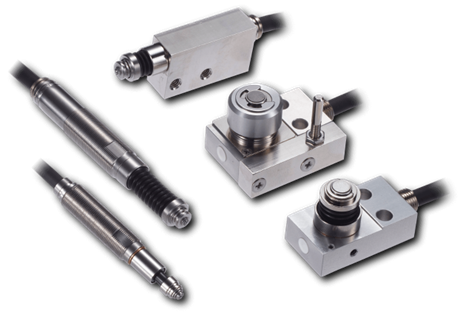
接触式の高精度スイッチで、工作機械やロボット、治具などの位置決めやワーク有無検出に用いられます。最大繰返し精度0.5µmと極めて高精度で、IP67の防水防塵性能を備え、悪環境下でも安定動作します。200種類以上の標準モデルがあり、狭所対応、高温対応、真空対応、低接触力タイプなどバリエーションが豊富です。
ツールセッタ(工具長測定センサ)
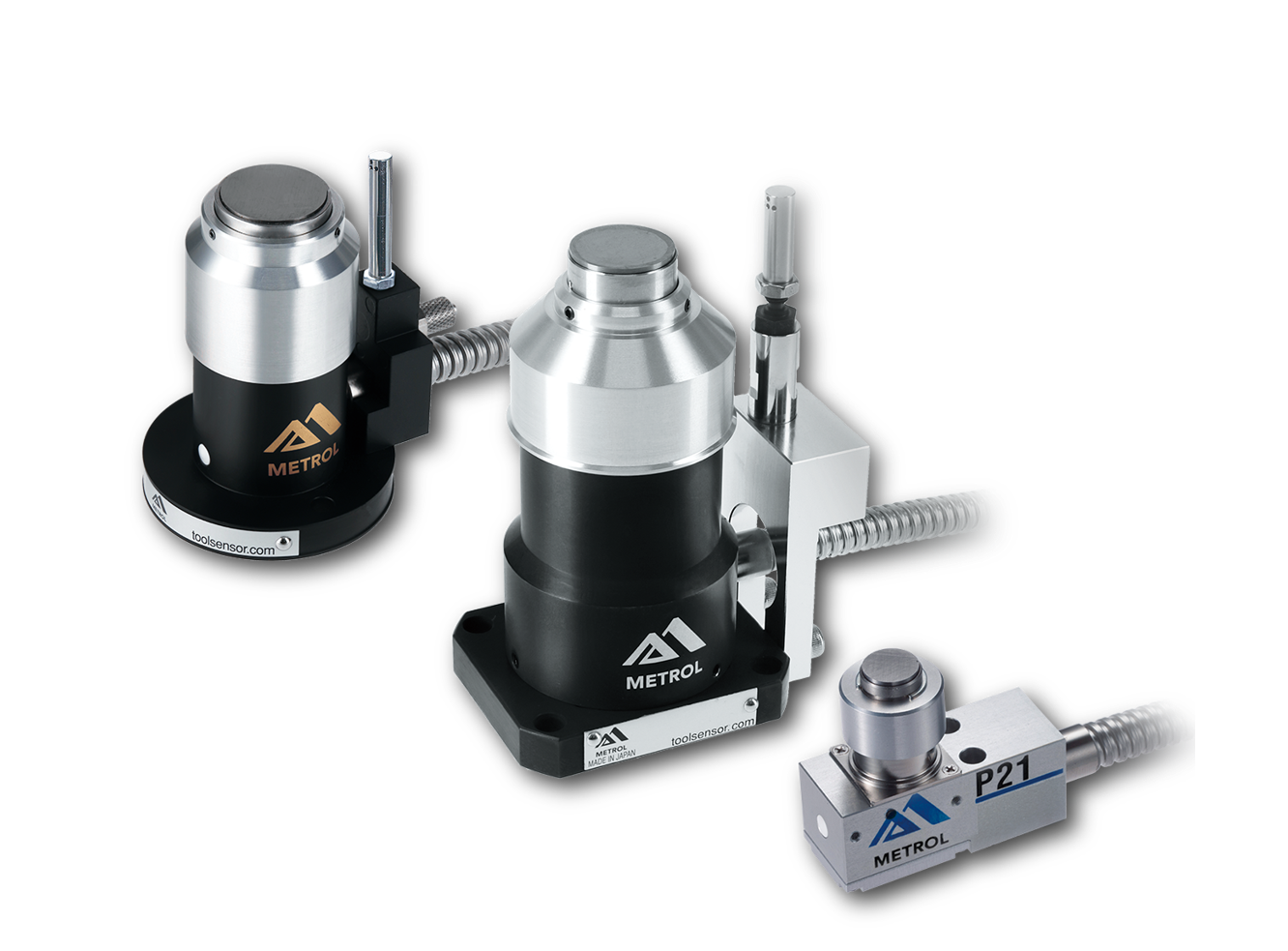
CNC工作機械や産業用ロボットに搭載し、工具長の測定や原点位置出し、工具折損検知などに使用される接触式センサです。工具の長さや摩耗、熱変位を機内で自動測定・補正することで加工不良を防止し、段取り時間を大幅短縮します。世界74ヵ国で50万台以上の出荷実績があるメトロールのベストセラー製品です。
タッチプローブ(機上測定プローブ)
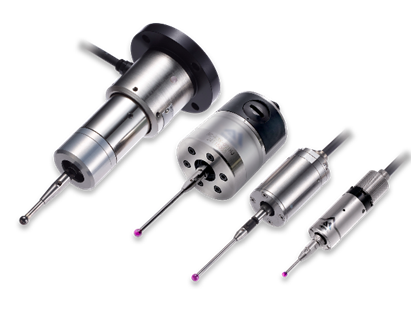
工作機械やロボットに搭載し、加工前のワーク位置決め(芯出し)や加工後の寸法測定を自動で行う機内計測用の接触式プローブです。繰り返し精度1µmでワークの基準出し・寸法検査を自動化します。有線式と無線式(ワイヤレス)のモデルがあり、5軸加工機やロボットへの後付けニーズにも応えています。
エアマイクロセンサ(空圧式センサ)
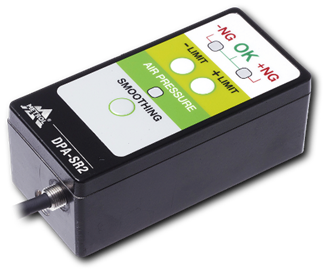
空気圧を利用した非接触センサで、ワークの着座状態を数ミクロン精度で検出できます。従来は困難だった10µm以下の隙間(「浮き」)を±0.5µmの繰返し精度で検知し、ワークと治具の密着不良による加工不良や設備のダウンタイム発生を防止します。半導体製造プロセスや精密部品のクランプ工程、研削盤の砥石位置合わせなどで活用され、国際標準のIO-Link通信にも対応したスマートセンサです。
関連記事
切削加工時のワーク浮き上がり検出で、加工不良品を未然に防止
CNCマシニングセンタでエンジン部品を切削加工されていましたが、 ワークの着座不良による加工不良品の発生でお困りでした。
メトロールの『エアマイクロセンサ〈ショートレンジ形〉』は、±0.5µm繰返し精度で、切粉の挟み込みによる、治具とワークの10µmの僅かな浮き上がりを確実に検出。機械を自動でストップし、加工不良の発生を未然に防止します。
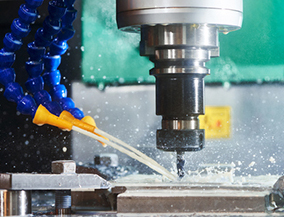
切削工具 折損の基本。加工条件設定とよくある課題
代表的な切削用工作機械として、「旋盤」について解説します。
1. 基本理解
2. 折損の基本要因
3. 折損パターンの種類
4. 折損防止のための加工条件設定
5. よくある問題と解決策
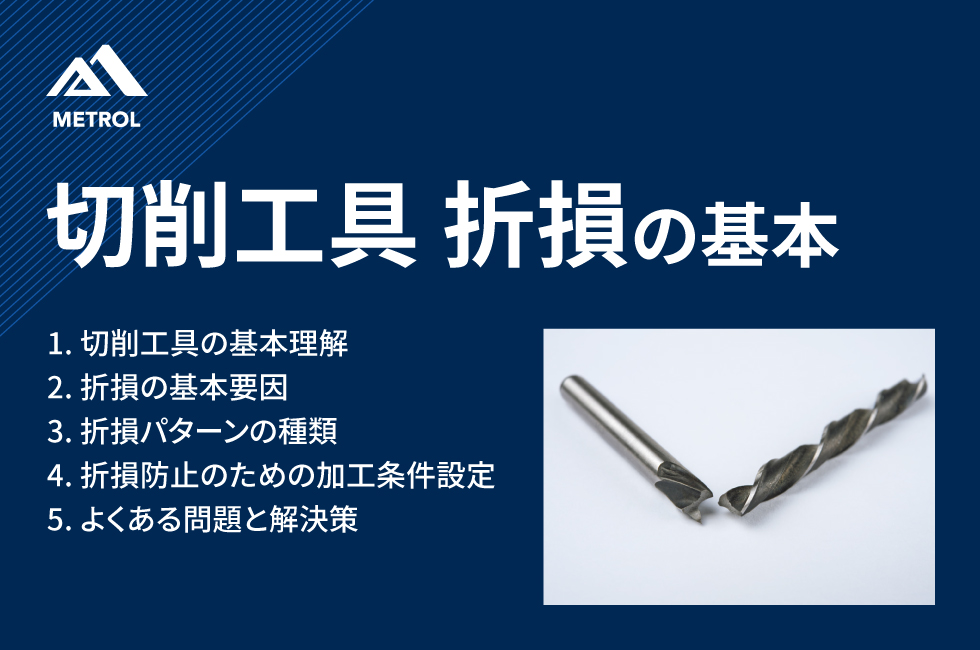
ロボットのハンド交換でタッチプローブを活用。ワークの原点出し・計測を自動化
ロボットアームにメトロールの『タッチプローブ』を持たせることで、ワークの外径・内径、高さを希望の仕様に自動で加工できるように。
・原点出しの精度があがり加工精度が向上
・加工後の計測自動化で作業者の検査工数が大幅短縮
など生産性の向上につながります。
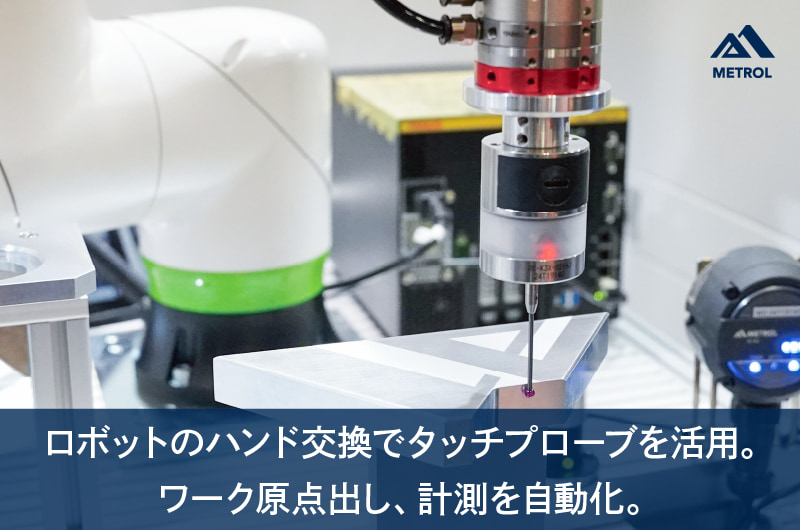