マイクロメーターとは?基本から測定手順まで
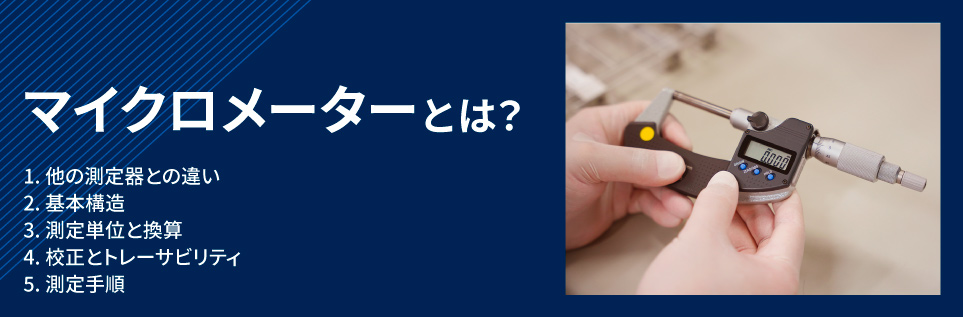
マイクロメーターは、外径や厚みをミクロン単位で正確に測れる精密測定器です。
本記事では、基本構造や測定手順、ノギスやダイヤルゲージとの違いまで分かりやすく解説し、高精度センサ技術など最新の計測ソリューションもあわせてご紹介します。
目次
マイクロメーターとは
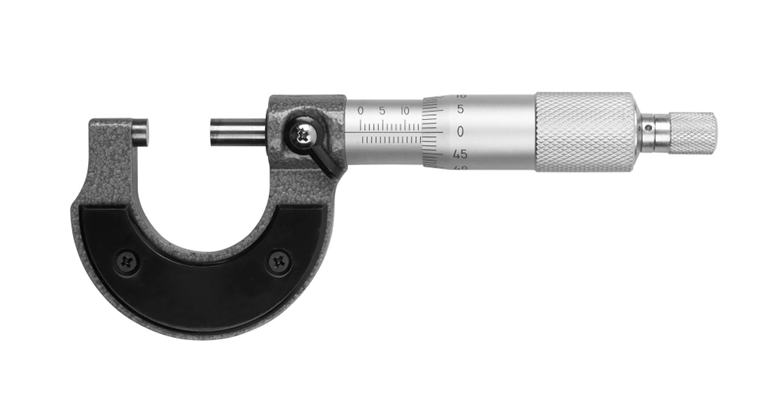
マイクロメーターとは、精密なねじ機構を利用して対象物の外径や厚みなどを高精度に測定するための測定工具です。フレームの間に測定物を挟み込み、回転ねじによるスピンドル(測定軸)の微小な軸方向移動量で寸法を読み取ります。
一般的なアナログのマイクロメーターではねじのピッチ(山と山の間隔)が0.5mmに設定されており、シンブル(目盛の付いた回転部)1回転あたり0.5mmだけスピンドルが進む構造です。
この回転角度と移動量の関係を利用して、1回転を50等分した目盛、つまり通常0.01mm単位で読み取りが可能となり、肉眼では測れない微小な長さを拡大して測定できます。
マイクロメーターの最小表示量は、アナログ式で一般に0.01mm、デジタル式では0.001mm(1μm)が標準的です。
一般的なコピー用紙の厚さが0.09mmなので、非常に精密な測定ができることが実感できます。
ノギス・ダイヤルゲージなど、他の測定器との違い
マイクロメーターと用途が似た代表的な測定器としてノギス(キャリパ)やダイヤルゲージがあります。
ノギスとの比較
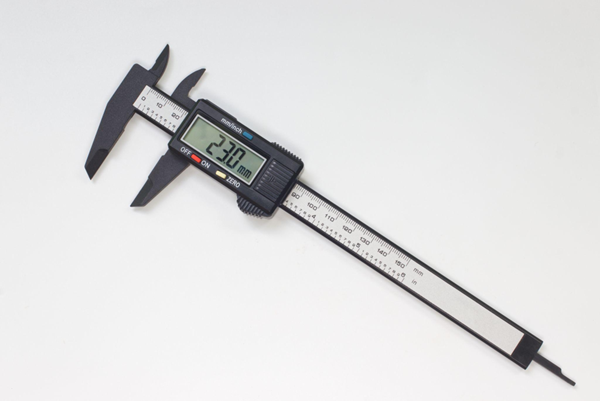
ノギス(一般的なデジタル/アナログノギス)は本体のスライダを動かして外径・内径・段差・深さなど様々な寸法を直接測定できる万能測定器です。
ノギスはその構造上、測定単位は0.1mm程度に留まりますが、最小目盛りは0.02mmや0.05mmとなっています。
それに対し、マイクロメーターは対象物の寸法に応じた専用形状(外側用、内側用、深さ用など)のものを選ぶ必要がありますが、ノギスよりも高い精度で測定するために設計された工具です。
ダイヤルゲージとの比較
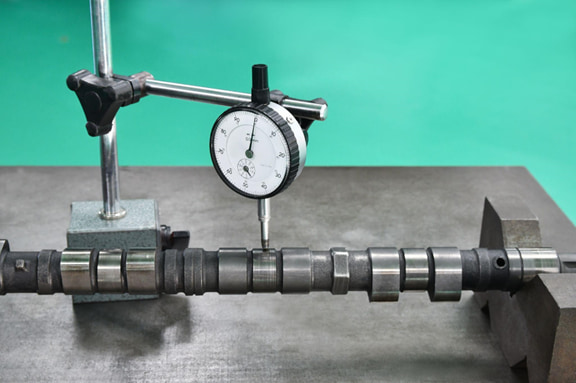
ダイヤルゲージは主に比較測定に用いられる測定器で、単体では寸法を測定できないため「スタンド」などの固定器具が必要です。
ダイヤルゲージは軸方向の微小変位を針の回転で拡大表示するもので、機械の振れや歪み量など幾何公差の測定に適しています。
これらの違いは、ノギスやマイクロメーターが「絶対寸法を直接読み取る」測定器であることに対し、ダイヤルゲージは分解能や繰り返し精度が高く「ゼロセットされた基準からの差を読み取る」比較器であることです。
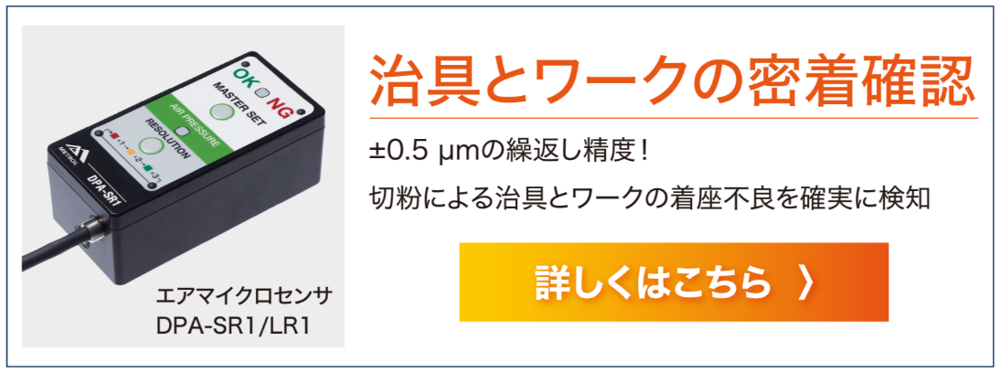

マイクロメーターの構成と構造
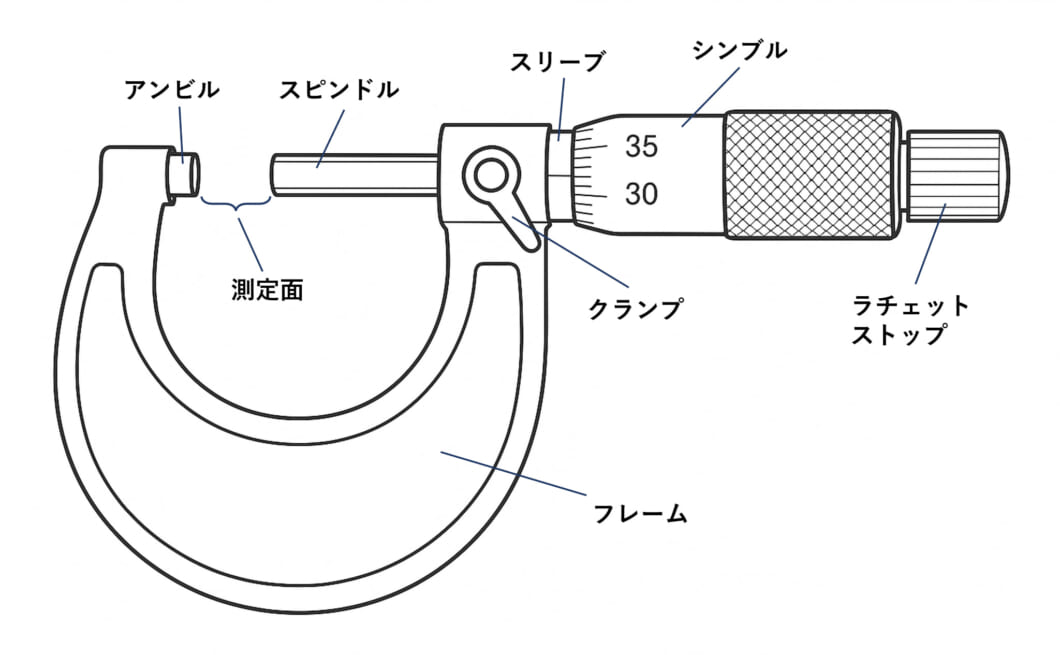
マイクロメーターは一見シンプルな形状ですが、精密測定を可能にするいくつかの部品で構成されています。中でも主要な部品について説明いたします。
部品名 | 説明 |
---|---|
アンビル | フレーム先端に固定された測定面で、対象物に直接当てる円盤状の金属面です。 |
スピンドル | アンビルと向かい合うもう一方の測定面を持つ可動軸で、シンブルの回転によって軸方向に前進・後退します。 |
スリーブ | フレームに固定された円筒部分で、外周に均等な主目盛(基準目盛)が刻まれています。 |
シンブル | スピンドル後端に取り付けられた回転筒で、指でつまんで回すことでスピンドルを前進・後退させます。 |
ラチェットストップ | シンブルのさらに後端にある小さなノブで、一定以上のトルクで回そうとするとカチカチと空回りする仕組みになっています。 |
構造上の特徴
マイクロメーターは構造上、アッベ誤差や余弦誤差を極力抑えた設計になっています。アッベの原理により目盛軸と測定軸が一直線上に配置されており、ノギスのようなスライド式に比べ角度の影響(余弦誤差)が生じにくいという利点があります。
適切な姿勢でラチェットストップを用いて測定することで、これらの構造上の精度を十分に引き出すことができます。
アナログ式とデジタル式
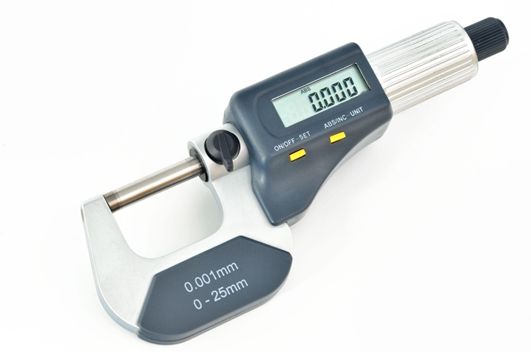
マイクロメーターには昔ながらのアナログ式(機械式)と、液晶に数値を表示するデジタル式があります。基本構造はどちらも同じで、ねじによるスピンドルの送りで寸法を測定する点は共通です。
違いは測定値の表示方法で、アナログ式ではスリーブとシンブルの目盛を人間が読み取るのに対し、デジタル式では内部のスケールが検出した移動量を電子的にカウントし、LCD(液晶ディスプレイ)上に数字で表示します。
デジタル式の内部検出にはロータリエンコーダやリニアスケール(電磁式や静電容量式などメーカーによって方式は様々)が用いられ、シンブルを回した角度(または直進量)を電気信号に変換して演算することで高分解能の読取りを実現しています。
測定単位と換算
マイクロメーターで扱う寸法単位は主にミリメートル(mm)およびマイクロメートル(μm)です。
単位の換算は以下の関係があります。
1mm = 1000μm
1μm = 0.001mm
1μmは非常に小さい単位で、人間の髪の太さがおよそ80μm程度であることからも1μmの微細さが理解できるでしょう。
マイクロメーターで読み取った値は通常mm単位で報告されますが、品質管理上さらに細かく評価する場合や公差表示などではμm単位が用いられることもあります。
例えば「12.72mm」と測定した場合、「12.72mm = 12,720μm」であり、公差±5μmなどという表現と組み合わせて表記されることがあります。
校正とトレーサビリティ
どんなに優れた測定器でも、適切に校正されていなければ信頼できる測定結果は得られません。校正とは「測定器の示す値を、より高精度な標準器と比較して誤差を把握し、必要に応じ調整すること」を指します。
マイクロメーターの場合、通常はブロックゲージ(長さの基準器)を用いて、例えば5mm、10mm、15mm…といった既知の長さを測り、示された値との差を確認します。
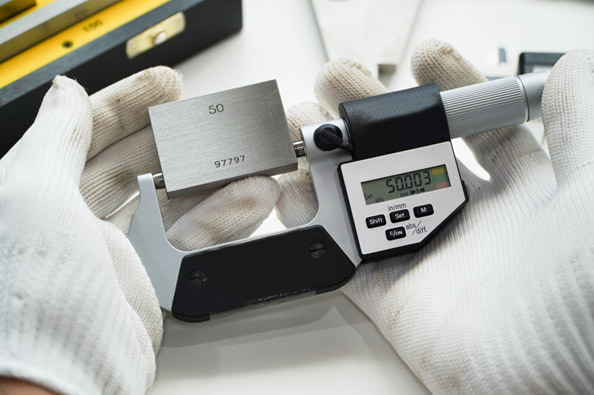
こうした校正作業により、そのマイクロメーターが規格内の精度であることを証明し、測定値の信頼性を担保します。
特に品質保証の場面では測定結果のトレーサビリティ(追跡可能性)が重要で、「その測定器がどのような標準器で校正されたか」を明らかにすることで、得られた寸法値が国家標準に結び付いた信頼できるものであることを示します。
測定結果が国際的に通用するには、この計量トレーサビリティの確立が不可欠です。
ブロックゲージは現場用と校正用を区別しておく
ブロックゲージはとても高価で、起業したての会社や規模の小さな町工場では「加工現場で使用するもの」と「校正専用のもの」を揃えておくのが難しいものです。
そのため、現場で使用している「摩耗したブロックゲージ」をそのままマイクロメーターの校正に使用している会社は少なくありません。
品質保証の観点からもこれは推奨できない行為であり、顧客からの信用を失う可能性があることなので、必ず校正用のブロックゲージを準備しておいてください。
校正用ブロックゲージは恒温室(検査室)内で保管・使用する
校正用のブロックゲージを用意しても、温度変化の激しい現場で保管・使用していては意味がありません。
正確な寸法管理には、常温で保たれている「恒温室」が必要不可欠です。加工の現場とは区別した「検査のための部屋」を設置しましょう。
校正用のブロックゲージを恒温室で使用・保管することで、四季や天候による温度変化の影響を最小限にし、測定器具・測定値の信頼性を担保できます。
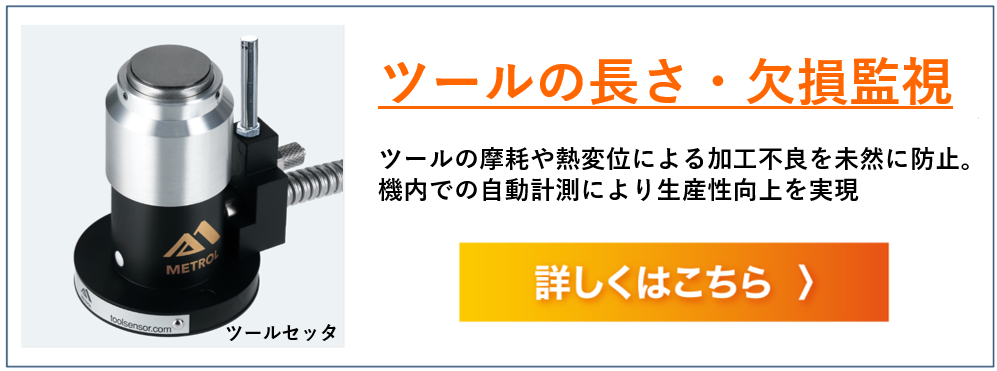

正しい測定手順
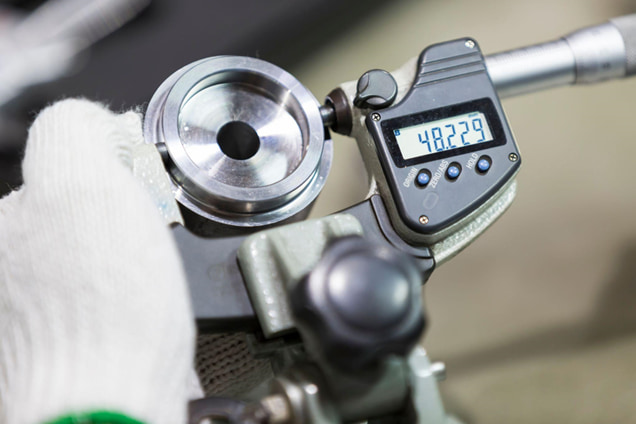
最後に、マイクロメーターを用いた正しい測定手順について、基本的な流れをまとめます。
精密測定では「正しい方法で使う」ことが精度確保の大前提となるため、一つ一つの手順を丁寧に実施しましょう。
①温度馴染みの徹底
測定物とマイクロメーター本体を使用環境の温度に十分馴染ませます。
例えば屋外から持ち込んだ部品や冷却後の部品は内部温度が周囲と異なるため、そのまま測ると温度変化中に寸法が刻々と変わってしまいます。
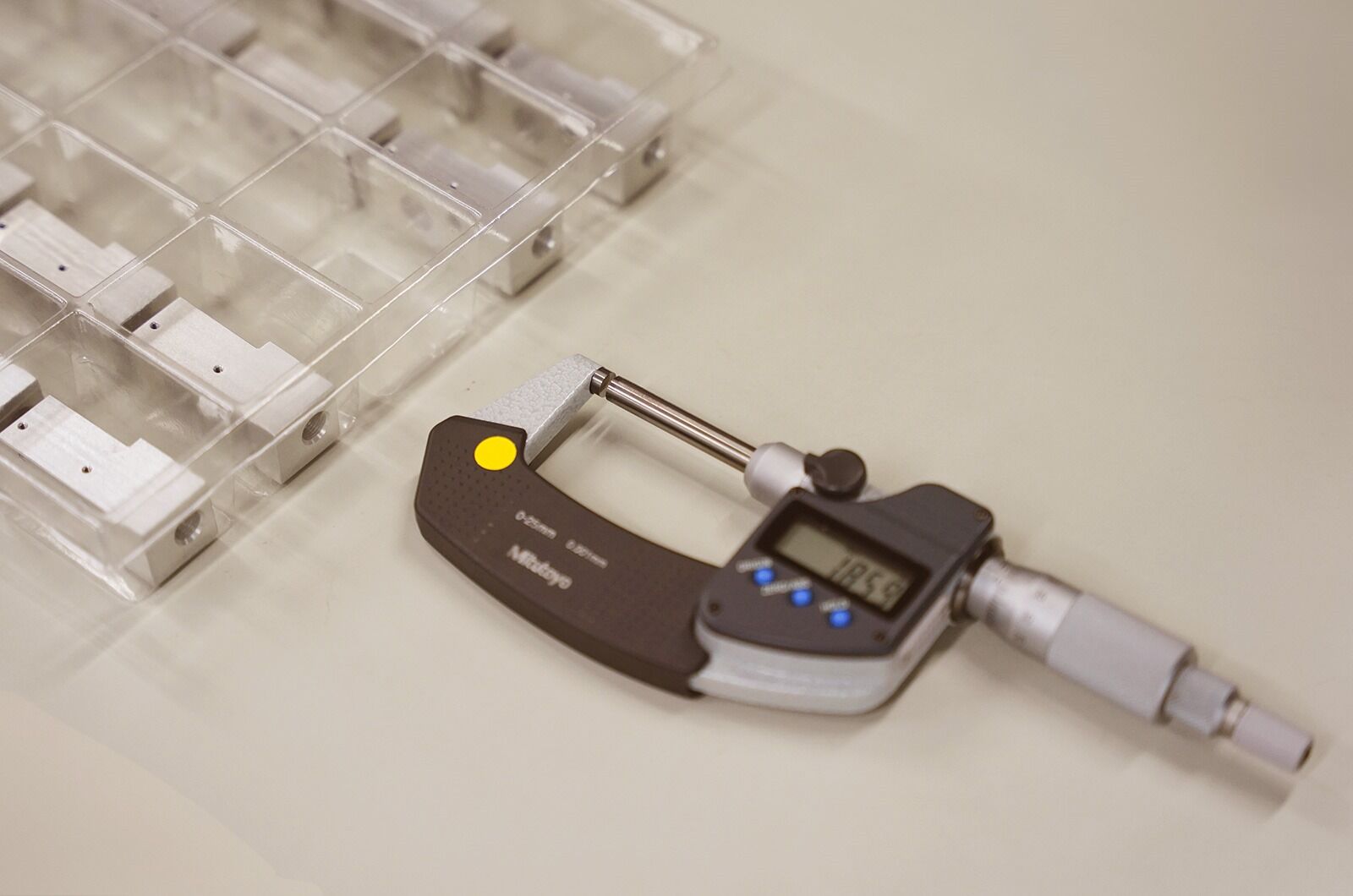
②測定面の清掃
アンビルとスピンドル先端の測定面を清潔にします。乾いた清潔な紙や布を両面に挟み、軽く拭き取るように引き抜いて埃や微細なゴミを除去します。
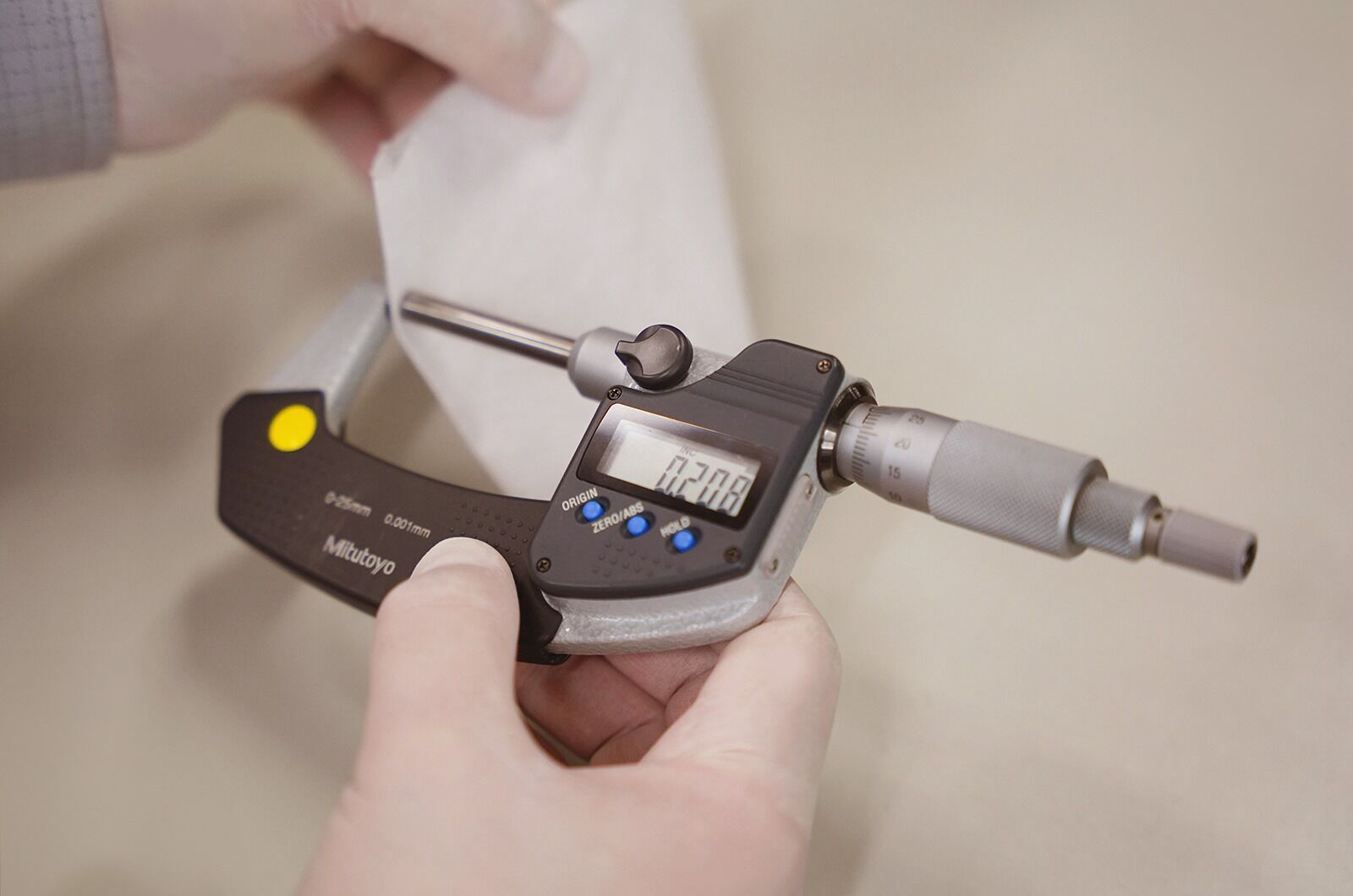
③ゼロ点の確認(原点合わせ)
測定前には必ずマイクロメーターのゼロ点をチェックします。
まずラチェットストップを使ってアンビルとスピンドルをゆっくり閉じ、測定面同士を軽く当接させます。
ラチェットが空転し始める「カチッ」という感触が適正圧の合図です。
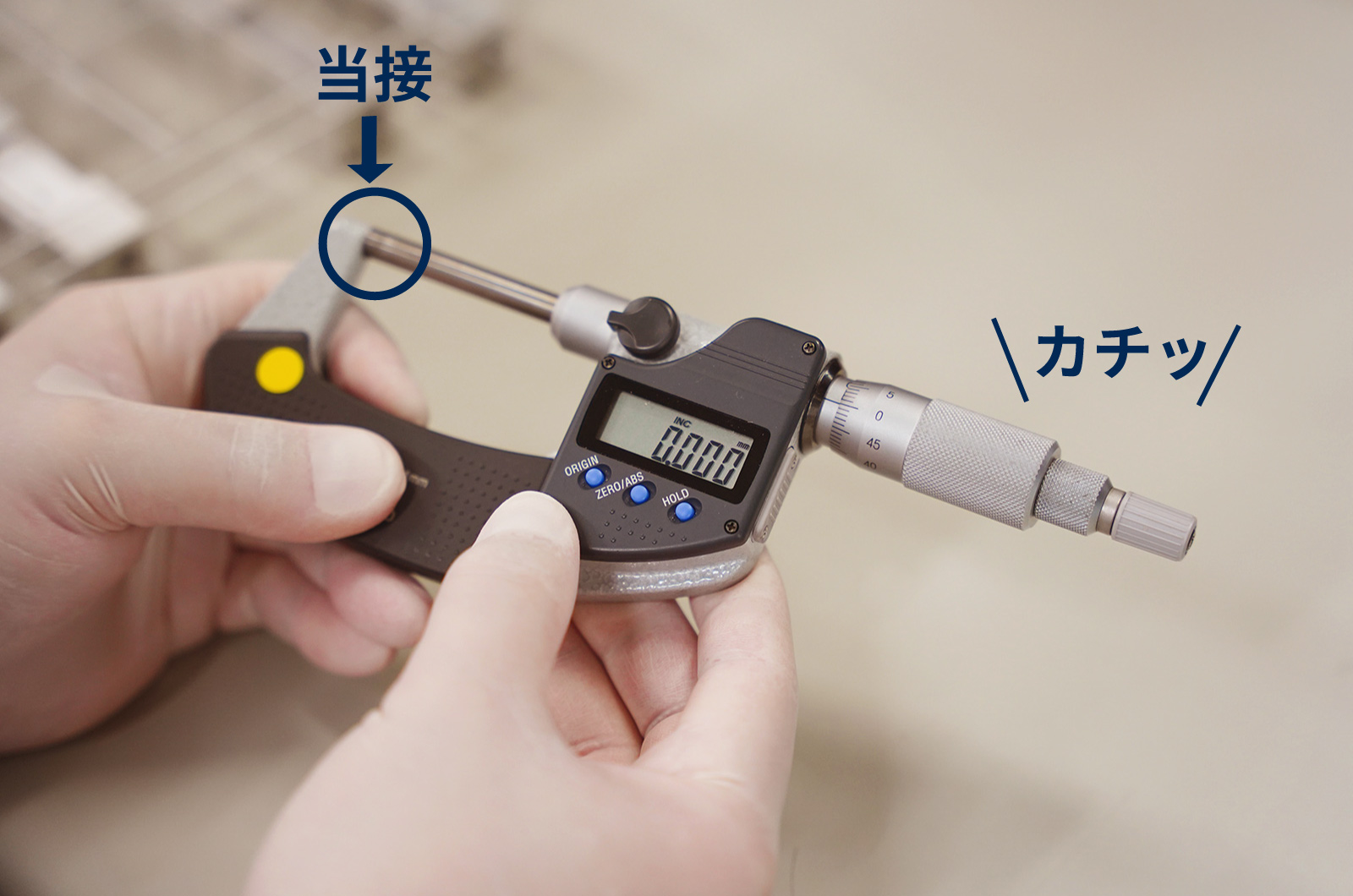
④測定の実施
いよいよ対象物の測定です。測定物をアンビルとスピンドルの間にまっすぐ挟み、シンブルを回してゆっくりと閉じていきます。
測定面が当たったら、ゼロ点確認と同じ姿勢・力加減でラチェットストップを3~5回ゆっくりと回し、適切な測定圧をかけます。
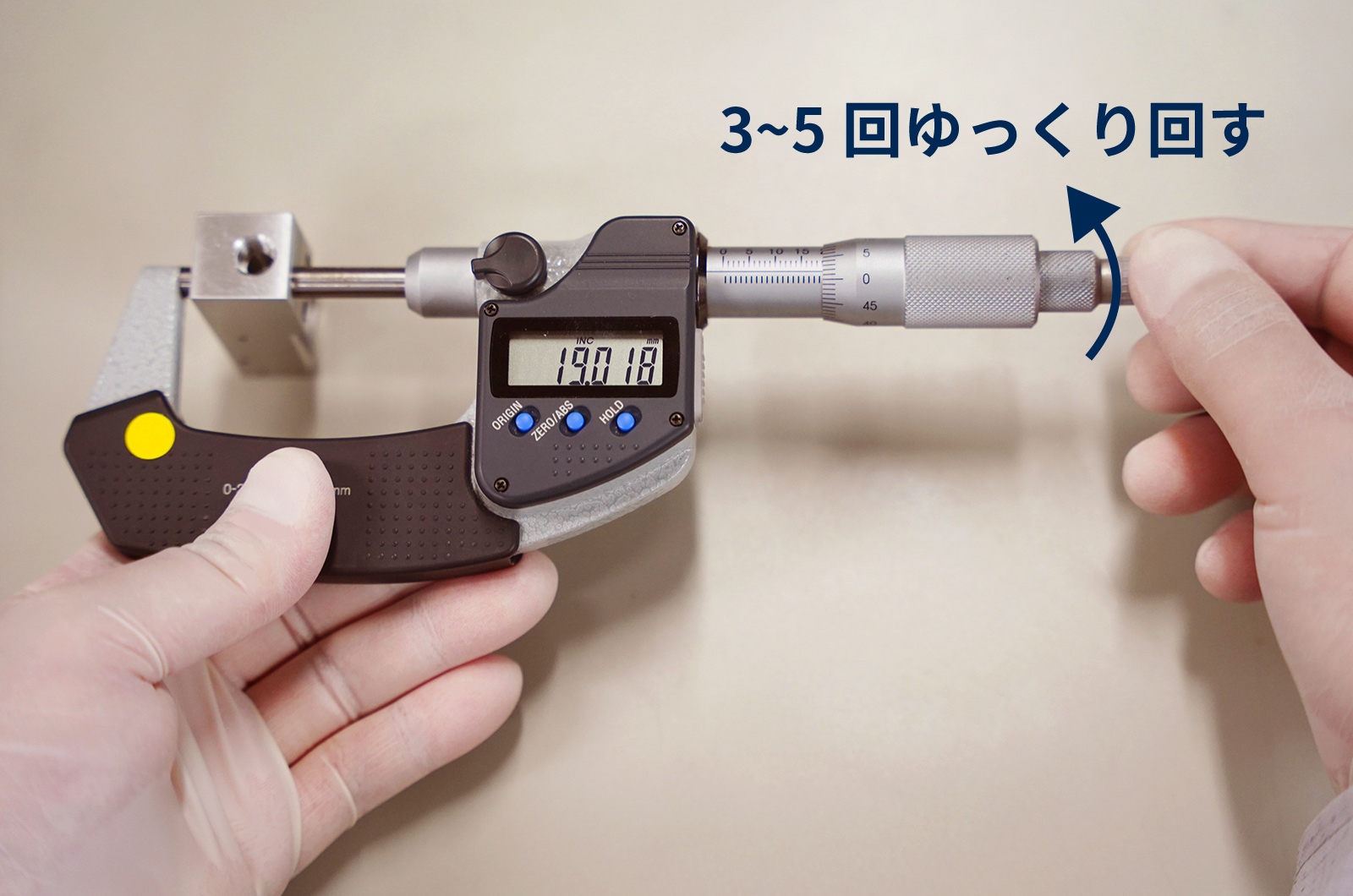
⑤目盛の読み取り
シンブルとスリーブの目盛を正確に読み取ります(デジタル式なら表示を読み取ります)。
アナログ式の場合、スリーブの目盛を見て、露出している最後の数値(例:19mmなら「19」まで見えている状態)を読み取ります。次に、スリーブの基準線と重なっているシンブルの目盛を読み取り(例:「1」なら0.01mm)それらを合計した値が測定値( 例: 19+0.01=19.01で測定値は「19.01mm」)です。もし、基準線とシンブルの目盛が重なっていない場合には、基準線下側の目盛を読み取り合計した値が測定値となります。
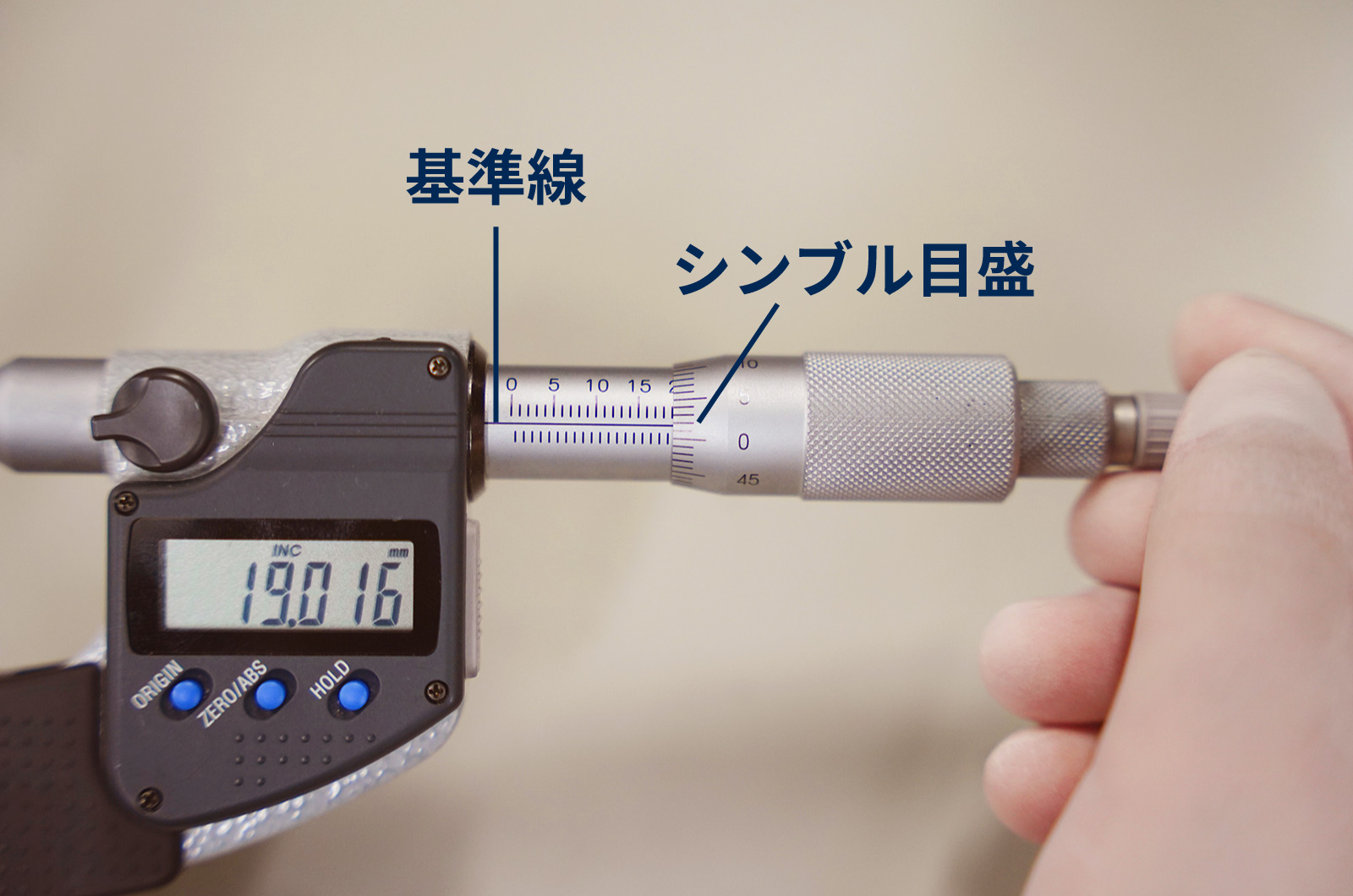
⑥測定後の処置
測定が終わったら、スピンドルを少し開いて測定物を取り出します。複数箇所を測る場合は以上の手順を繰り返します。
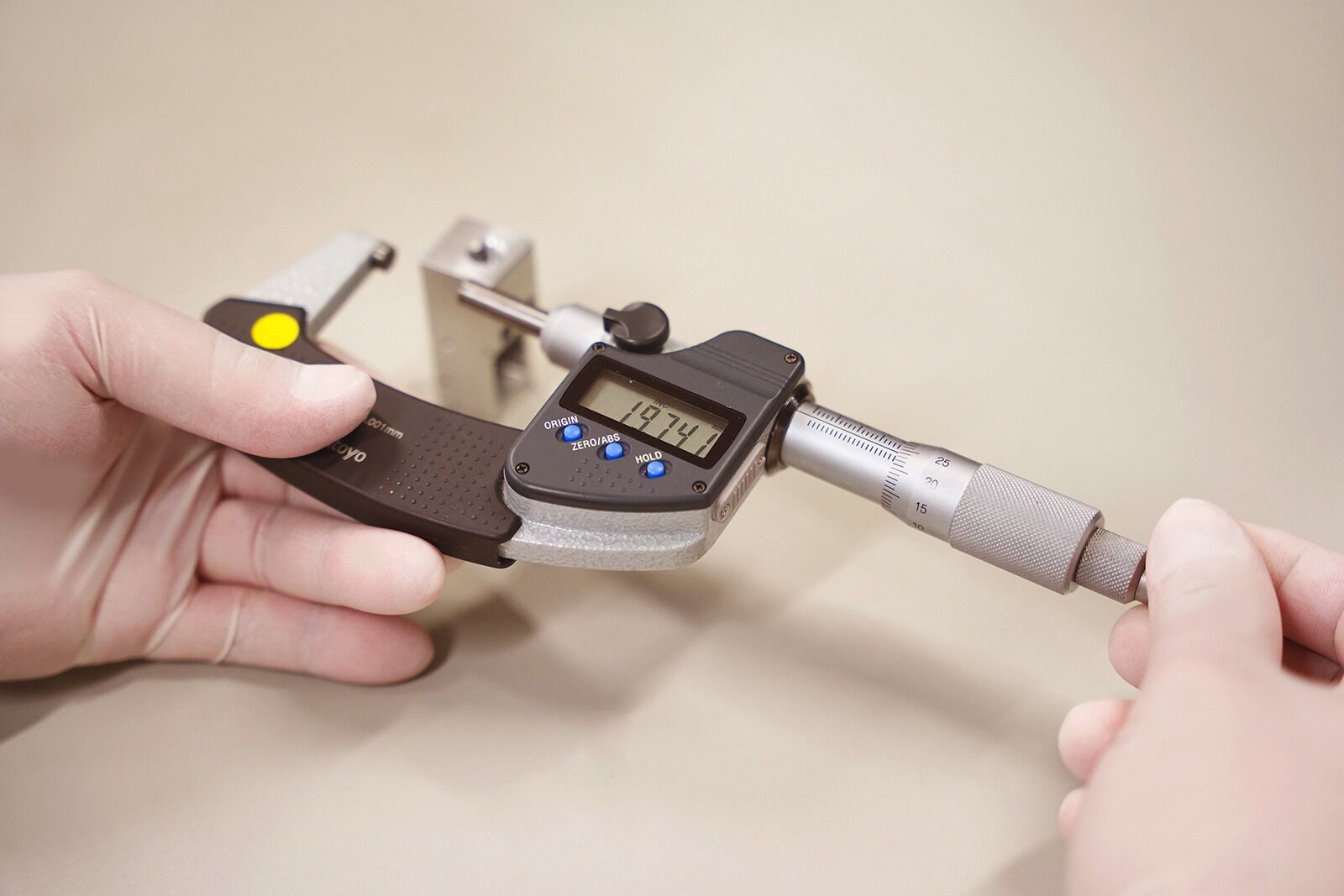
メトロールの高精度な位置決めセンサとは?
微細寸法を正確に測定できるマイクロメーターですが、測定者の熟練度や使用環境に左右されやすい点が課題とされてきました。
そこで注目されているのが、より安定した計測を可能にするセンサー技術や測定ソリューションです。とくに、工作機械のゼロ点検出や位置決めなど、超精密な測定・制御を得意とする企業として知られているのがメトロールです。
高精度位置決めタッチスイッチ(位置決めセンサ)
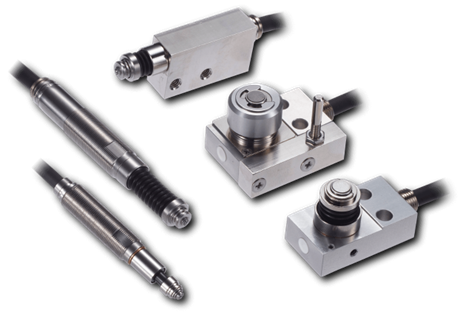
接触式の高精度スイッチで、工作機械やロボット、治具などの位置決めやワーク有無検出に用いられます。最大繰返し精度0.5µmと極めて高精度で、IP67の防水防塵性能を備え、悪環境下でも安定動作します。200種類以上の標準モデルがあり、狭所対応、高温対応、真空対応、低接触力タイプなどバリエーションが豊富です。
ツールセッタ(工具長測定センサ)
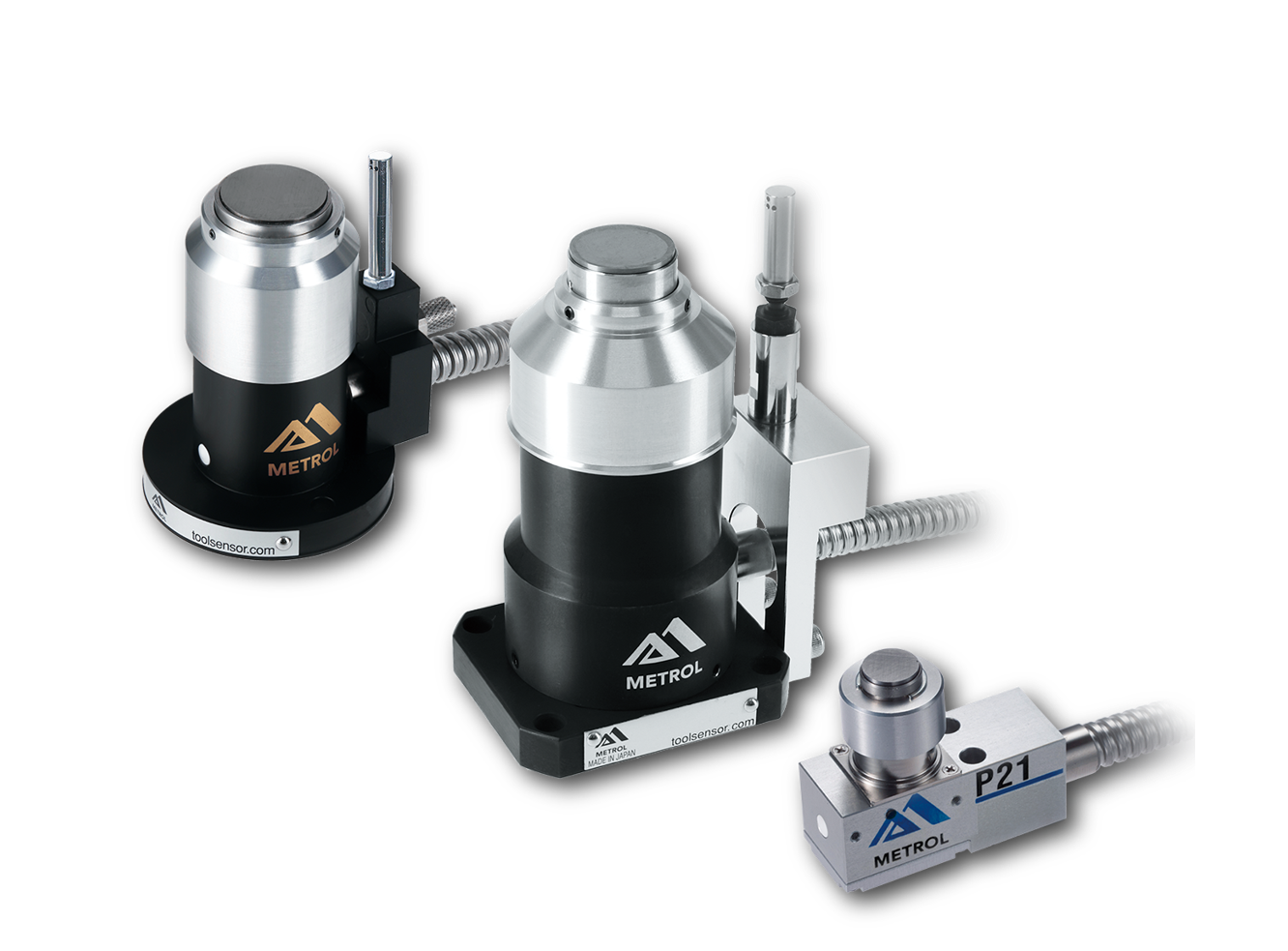
CNC工作機械や産業用ロボットに搭載し、工具長の測定や原点位置出し、工具折損検知などに使用される接触式センサです。工具の長さや摩耗、熱変位を機内で自動測定・補正することで加工不良を防止し、段取り時間を大幅短縮します。世界74ヵ国で50万台以上の出荷実績があるメトロールのベストセラー製品です。
タッチプローブ(機上測定プローブ)
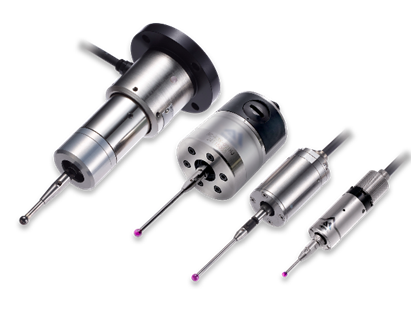
工作機械やロボットに搭載し、加工前のワーク位置決め(芯出し)や加工後の寸法測定を自動で行う機内計測用の接触式プローブです。繰り返し精度1µmでワークの基準出し・寸法検査を自動化します。有線式と無線式(ワイヤレス)のモデルがあり、5軸加工機やロボットへの後付けニーズにも応えています。
エアマイクロセンサ(空圧式センサ)
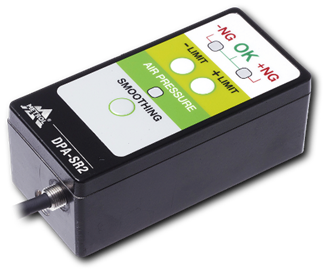
空気圧を利用した非接触センサで、ワークの着座状態を数ミクロン精度で検出できます。従来は困難だった10µm以下の隙間(「浮き」)を±0.5µmの繰返し精度で検知し、ワークと治具の密着不良による加工不良や設備のダウンタイム発生を防止します。半導体製造プロセスや精密部品のクランプ工程、研削盤の砥石位置合わせなどで活用され、国際標準のIO-Link通信にも対応したスマートセンサです。
関連記事
タッチプローブによる研削盤の「機上測定」とは?
ワークの仕上げ加工の品質を握る「CNC平面研削盤」。
「三次元測定機など測定のための段取り作業や移動に時間がかかる…」
「測定のやり方が人によってばらつく…」
「測定後の手戻りと追加工をやめたい…」
タッチプローブによりこれらの課題が解決します。
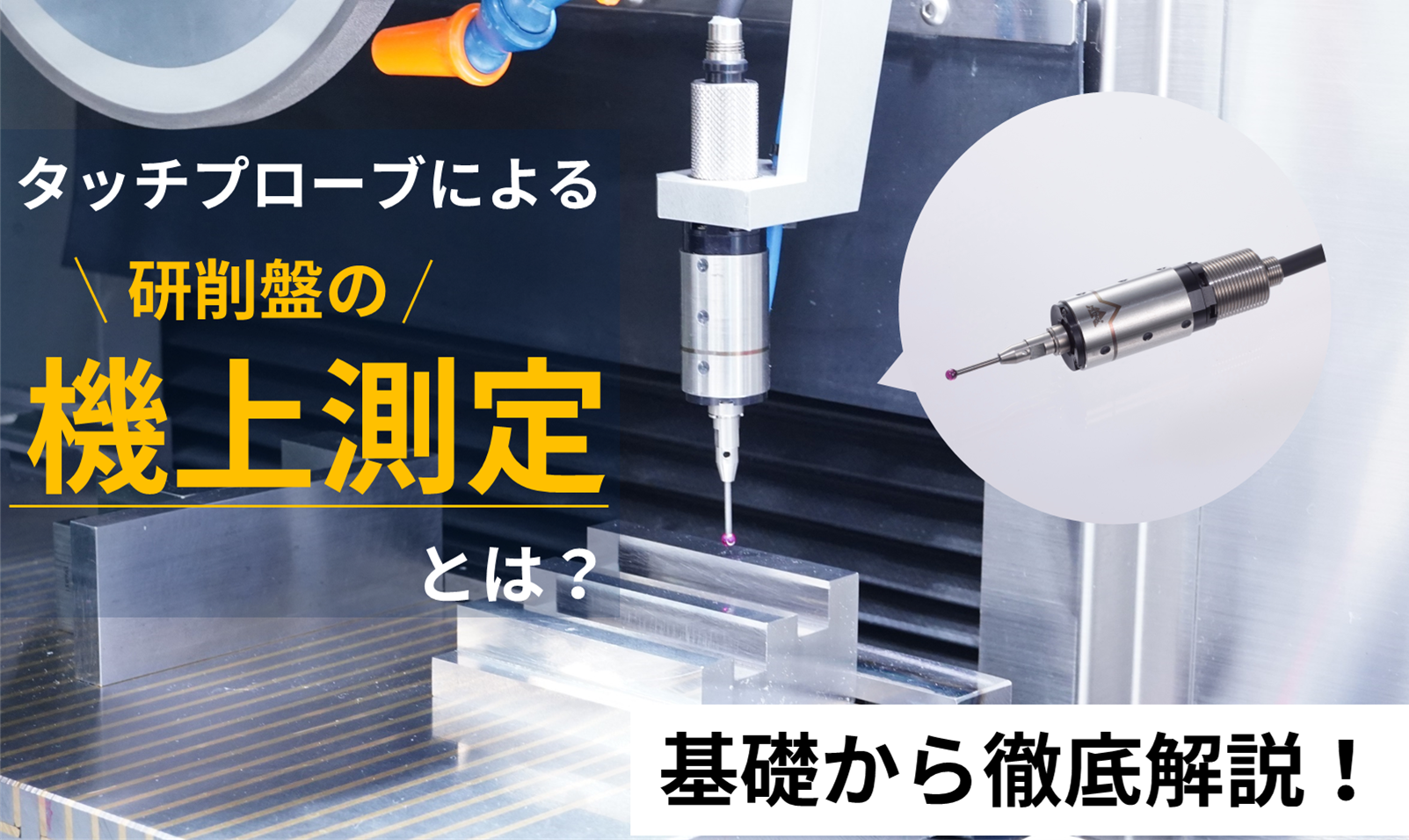
「ピンゲージやシリンダーゲージを使った内径測定の時間を短縮したい」
「低コストで内径検査(ポカヨケ)を自動化したい」
「作業者ごとの測定結果のバラつきを無くし、誰でも簡易的内径測定を行いたい」
これらの課題を解決する「エアマイクロセンサ」を使った検査方法の概要と仕組みについて解説します。
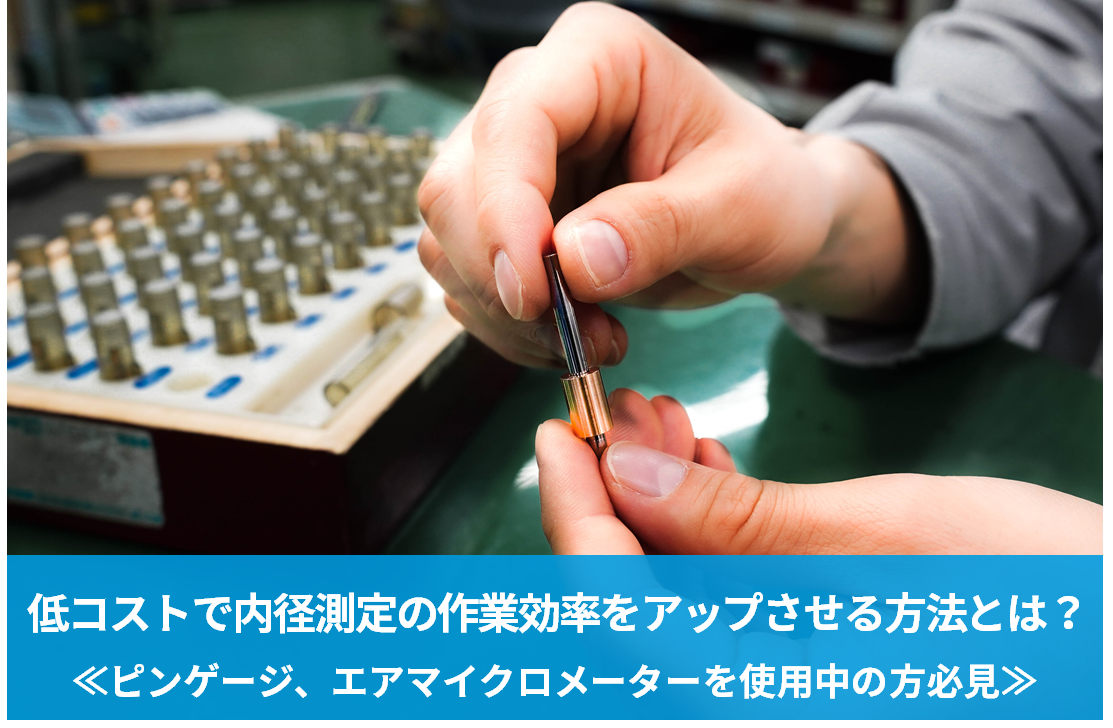
「エアマイクロメーター」からの置き換えで、大幅コスト削減
メトロールの「エアマイクロセンサ」は、−NG/OK/+NGの許容公差設定で、3クラスを良否判別できます。
NCからの外部入力にも対応し、マスターセットボタンを押さずに、公差リミット値の設定も可能です。
高額な「エアマイクロメーター」での内径判別が、約1/4の低コストで簡単にできます。
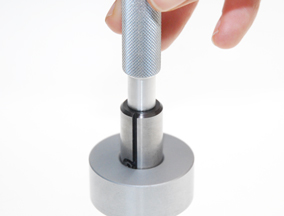
電池フィルムのミクロンレベルの厚みを、非接触で安定計測
従来、「マイクロゲージ」による測定は、作業者の測定圧による個人差が大きく、精度の求められるミクロンレベルの電池フィルム厚の測定には不向きです。
メトロールの「エアマイクロセンサ」は、独自開発の空圧回路を搭載した、非接触式のエアセンサ。
高精度ON/OFF位置信号をサーボモータで読み取ることで、50μmのフィルムの厚さを、±0.5μmの繰返し精度で安定して測定する事が可能になります。
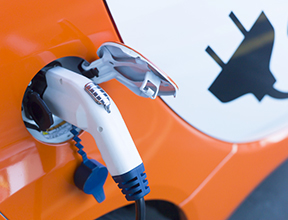